Corrosione
Il termine corrosione (dal latino com- particella indicante insistenza e rodere, per "consumare"[1]) indica un processo naturale e irreversibile di consumazione lenta e continua di un materiale, che ha come conseguenze il peggioramento delle caratteristiche o proprietà fisiche del materiale inizialmente coinvolto. La corrosione è un fenomeno di natura elettrochimica che determina una interazione chimico-fisica del materiale metallico con l'ambiente che lo circonda.
Possono essere coinvolti da tale fenomeno molti tipi di materiali, sebbene il termine "corrosione" venga comunemente associato ai materiali metallici (cioè i metalli e le loro leghe). La corrosione dei metalli può essere definita come un processo di degradazione e ricomposizione con altri elementi presenti nell'ambiente: metalli e leghe si trovano a un livello energetico maggiore di quello a cui stanno i corrispondenti minerali, per cui sotto determinate condizioni ambientali tendono a riprendere lo stato più stabile presente in natura, usualmente quello di ossido, di idrato o di sale.
Trattazione elettrochimica dei fenomeni corrosionistici
[modifica | modifica wikitesto]
A prescindere da quale sia il particolare meccanismo scatenante, affinché la corrosione abbia luogo è necessario che intervengano dei processi di natura elettrochimica a cui prendano parte il materiale metallico (che funge da elettrodo) e l'ambiente di corrosione (che funge da elettrolita).[2] Il sistema così costituito può essere schematizzato con una cella galvanica in condizioni di corto circuito, cioè una cella galvanica in cui gli elettrodi sono da una parte separati dall'elettrolita (all'interno del quale si ha trasporto di carica elettrica per mezzo di ioni) e dall'altra parte sono in contatto attraverso un circuito elettrico esterno (dove il trasporto di carica è assicurato dal moto di elettroni).[3]
La corrosione è provocata dallo svolgersi di una reazione di ossidazione, che ha luogo all'anodo della cella che rappresenta il sistema corrosionistico, mentre al catodo ha luogo una reazione di riduzione. In tutti i processi corrosivi, oltre a una semireazione di ossidazione del materiale metallico, ha luogo una semireazione di riduzione. La specie chimica coinvolta nella semireazione di ossidazione è principalmente il metallo, mentre le specie chimiche coinvolte nella semireazione di riduzione dipendono dall'ambiente di reazione.
La semireazione di ossidazione può essere schematizzata nel modo seguente:[3]
M → Mz+ + z e-
In cui z è la carica dello ione metallico (Mz+) che si forma in seguito all'ossidazione del metallo M, allontanando z elettroni (e-).
Oltre allo studio della cella elettrochimica rappresentativa del fenomeno, durante le indagini dei fenomeni corrosionistici vengono impiegati altri strumenti teorici sviluppati nell'ambito dell'elettrochimica, tra cui i diagrammi di Pourbaix (impiegati per mostrare l'effetto del pH sul fenomeno della corrosione una volta noto l'ambiente di reazione) e i diagrammi di Evans (utilizzati per ipotizzare la velocità di corrosione una volta noto lo stadio cineticamente determinante).
Ambiente di corrosione
[modifica | modifica wikitesto]La corrosione dei materiali metallici può essere classificata a seconda dell'ambiente in cui ha luogo la corrosione:[4][5]
- corrosione a umido: se avviene in presenza di acqua o di altro elettrolita;
- corrosione a secco: negli altri casi (ad esempio nell'ossidazione a caldo dei metalli o nell'ossidazione in atmosfera secca).
Meccanismi di corrosione
[modifica | modifica wikitesto]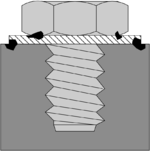
A seconda del meccanismo con cui avviene la corrosione, si parla di:[5]
- corrosione per attacco diretto (o corrosione chimica): se il materiale metallico è attaccato da particolari sostanze chimiche in presenza di acqua (sotto forma di acqua liquida o di vapore acqueo); un esempio di corrosione per attacco diretto è la corrosione dei materiali metallici esposti all'aria, denominata corrosione atmosferica;[6]
- corrosione elettrochimica: se la corrosione avviene tra due parti metalliche poste a contatto; se i metalli posti a contatto sono di natura differente, si parla in particolare di corrosione galvanica;[7]
- corrosione meccano-chimica: se la corrosione è causata dalla partecipazione di cause di natura elettrochimica e sforzi meccanici. Si possono distinguere ulteriormente:
- corrosione per sfregamento: se gli effetti della corrosione vengono esaltati dall'applicazione di forze di attrito, agenti sulla superficie del pezzo;
- tensocorrosione (o stress corrosion cracking): se gli effetti della corrosione vengono esaltati dall'applicazione di un carico costante nel tempo;
- corrosione per fatica: se gli effetti della corrosione vengono esaltati dall'applicazione di un carico variabile nel tempo.
Morfologia dei fenomeni corrosivi
[modifica | modifica wikitesto]A seconda della parte del materiale metallico interessata dalla corrosione, si parla di:[8]
- corrosione diffusa (o corrosione generalizzata): se tutta la superficie del materiale è interessata dalla corrosione;
- corrosione uniforme: se la corrosione interessa tutta la superficie del materiale e l'entità degli effetti corrosivi è uguale in ogni punto della superficie;
- corrosione disuniforme: se la corrosione interessa tutta la superficie del materiale e l'entità degli effetti corrosivi è più o meno accentuata in punti differenti della superficie;[9]
- corrosione localizzata: se la corrosione interessa solo alcune zone del materiale; la zona interessata dalla corrosione può presentare diverse morfologie, ad esempio:
- ulcere
- crateri
- caverne ("pitting cavernizzante")
- punte di spillo ("pitting penetrante")
- cricche (suddivise in intergranulari o transgranulari a seconda che le cricche seguano i bordi di grano o attraversino i grani cristallini);
- corrosione selettiva: se la corrosione ha luogo in zone specifiche del materiale. Si può ulteriormente distinguere:
- corrosione intragranulare (o cristallografica): si ha la corrosione di singoli grani cristallini)
- la corrosione intergranulare: avviene in corrispondenza dei bordi di grano
- corrosione interdendritica: associata a formazioni di forma dendritica all'interno del materiale;
- dealloying: consiste nella separazione dei componenti che costituiscono le leghe metalliche.
Corrosione intergranulare
[modifica | modifica wikitesto]La corrosione intergranulare (o intercristallina) si manifesta in corrispondenza dei bordi di grano di una soluzione solida, in particolare dell'acciaio inossidabile austenitico o ferritico che sia stato sensibilizzato con un riscaldamento oltre i 500 °C.
In queste condizioni infatti si ha la precipitazione dei carburi di cromo, i quali, grazie all'alta temperatura, diffondono verso le zone distorte (i bordi di grano), dove vi è una maggiore concentrazione di carbonio.
Si crea così una situazione in cui i bordi di grano sono ricchi di carburi di cromo, che fungono da catodo, e di matrice circostante con una percentuale di cromo minore del 12%, non più passivata e quindi fungente da anodo: può così avere luogo la corrosione a umido. Una grana fine in questa situazione è controproducente, in quanto una maggiore estensione dei bordi di grano implica maggiore estensione delle zone sottoposte a corrosione.
Per ridurre tale corrosione è consigliabile attraversare velocemente l'intervallo critico di temperatura (per esempio con raffreddamento in acqua) oppure prolungare il riscaldamento: questo per impedire o favorire la diffusione del cromo. Un'ulteriore soluzione, adottata spesso negli acciai inossidabili austenitici, consiste nell'aggiungere in lega quantità relativamente basse di metalli più carburabili del cromo (Ti, Nb o Ta), che, formando i propri carburi, impediscono la carburazione del cromo.
Una soluzione largamente diffusa consiste nel decarburare l'acciaio, portando la percentuale di carbonio al di sotto dello 0.03%, così da limitare la formazione di carburi di cromo. I materiali così costituiti sono contraddistinti dalla sigla "EL" (Extra Low Carbon), mentre un tenore percentuale di carbonio compreso tra lo 0.03% e lo 0.08% caratterizza acciai "L" (Low Carbon).
Corrosione per aerazione differenziale
[modifica | modifica wikitesto]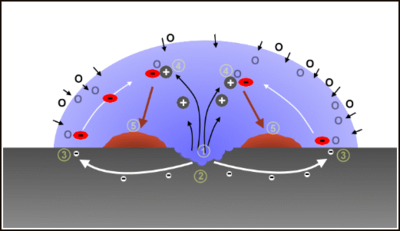
La corrosione localizzata per aerazione differenziale si instaura quando sulla superficie del materiale metallico sono presenti zone che presentano una differente permeabilità nei confronti dell'ossigeno.
La parte della superficie metallica meno permeabile all'ossigeno si comporta da regione anodica, quindi è sede del processo di dissoluzione del metallo; ad esempio nel caso dell'acciaio si ha il seguente processo di ossidazione:[3]
- Fe → Fe++ + 2e-
mentre la parte della superficie metallica più permeabile all'ossigeno si comporta da regione catodica, quindi è sede del processo di riduzione dell'ossigeno:[3]
- 1⁄2 O2 + H2O + 2e- → 2 OH-
Questo tipo di corrosione avviene nelle strutture metalliche interrate che attraversano strati di terreno di natura differente (ad esempio argilla, meno permeabile all'ossigeno, e sabbia, più permeabile all'ossigeno) o nel caso in cui la superficie del metallo sia parzialmente bagnata (essendo l'acqua poco permeabile all'ossigeno[3]), ad esempio all'interno di condotte idriche quando per un malfunzionamento dei dispositivi di sfiato si abbia la formazione di sacche d'aria.
Corrosione atmosferica
[modifica | modifica wikitesto]

In genere i materiali metallici esposti all'atmosfera e a temperatura ambiente tendono a corrodersi formando ossidi; la stabilità di tali ossidi diminuisce all'aumentare della temperatura. Ciò è dovuto al fatto che a temperatura ambiente quasi tutti i metalli hanno un'affinità chimica per l'ossigeno positiva, cioè tendono a reagire con l'ossigeno, ossidandosi.
In particolare, nel caso di una lega bimetallica, si hanno i seguenti casi:
- ossidazione del metallo soluto, se questo ha un'affinità per l'ossigeno maggiore e la diffusione di quest'ultimo nella lega è buona;
- ossidazione del metallo solvente: si forma uno strato di ossido del solvente con all'interno particelle del soluto;
- ossidazione di entrambi i metalli della lega.
Quindi da un punto di vista termodinamico la corrosione atmosferica è favorita. È possibile comunque sfruttare il fenomeno della passivazione per contrastare l'avanzare della corrosione. La passivazione di un materiale metallico consiste nella formazione di un film di ossido particolarmente stabile e sottile (dello spessore di qualche micrometro); la formazione di tale film dipende dalle condizioni esterne (tra cui umidità atmosferica e temperatura) e della natura del materiale metallico.
Nel caso in cui tale film riesca a bloccare la diffusione dell'ossigeno nel materiale metallico, si ha il fenomeno della passivazione; se invece tale strato di ossido non ricopre in maniera adeguata la superficie del materiale, l'ossigeno ha la possibilità di reagire con il metallo e il fenomeno della corrosione non viene bloccato.
Nel caso di rame o alluminio, l'ossido ha un peso specifico minore del peso specifico del metallo stesso, quindi a parità di peso l'ossido occupa maggior volume e protegge il materiale sottostante. Nel caso dell'acciaio, invece, l'ossido ha un peso specifico maggiore del peso specifico del metallo stesso, quindi, a parità di peso l'ossido occupa minor volume e si ritira e crea delle crepe dove penetra altro ossigeno che continua il processo corrosivo nella parte sottostante. Pertanto la pellicola di ossido di ferro (detta comunemente "ruggine"), essendo friabile e non sufficientemente aderente, non può essere considerata protettiva.
Aggiungendo all'acciaio altri metalli (come cromo e nichel) si riesce a ottenere una pellicola passivante molto aderente, ottenendo il cosiddetto "acciaio inossidabile".[10]
I fattori che intervengono sulla velocità di accrescimento dello strato di ossido sono:
- rapporto tra il volume dell'ossido che si forma e quello del metallo base ossidato, che determina lo stato del film di ossido: tensionato, in leggera compressione, raggrinzito;
- permeabilità all'ossigeno;
- conducibilità elettrica dell'ossido;
- all'aumentare della temperatura diminuisce l'energia liberata dal metallo nel processo di corrosione, quindi diminuisce l'energia che può passare all'ossigeno molecolare affinché si dissoci in ossigeno atomico e si leghi agli atomi metallici; in generale, comunque, la velocità di accrescimento dello strato di ossido aumenta con la temperatura, ma non sempre con andamento lineare; si preferiscono quindi metalli che obbediscono alle leggi logaritmiche e cubiche (alluminio e sue leghe, aggiunte di cromo).
Corrosione galvanica
[modifica | modifica wikitesto]Il meccanismo della corrosione galvanica[11] si produce secondo un processo a umido e si innesca quando due materiali, aventi un diverso valore di nobiltà (oppure due parti dello stesso materiale esposte a condizioni differenti), vengono posti a diretto contatto (formando un accoppiamento galvanico), in presenza su entrambi di un terzo elemento (detto "elettrolita").
Si viene a formare una cella galvanica in cortocircuito (detta macrocoppia) nella quale gli elettrodi sono costituiti dai due materiali accoppiati.
Si genera un flusso di elettroni dal materiale meno nobile (avente potenziale minore), denominato anodo (o polo negativo) che si ossida, verso quello più nobile avente potenziale maggiore, denominato catodo (o polo positivo), dove avviene la riduzione degli anioni, che può rivestirsi di strati metallici.
Le reazioni che avvengono durante il processo di corrosione sono tutte redox (dall'inglese reduction e oxidation). Per convenzione, il verso della corrente elettrica è assunto opposto al flusso degli elettroni, per cui si ha circolazione di una corrente continua di intensità i dalla zona catodica a quella anodica; la stessa corrente circola in verso opposto nell'elettrolita, trasportata dagli ioni disciolti.
I metalli meno nobili (per esempio zinco, ferro, nichel) presentano una maggiore tendenza a corrodersi rispetto ai metalli più nobili (per esempio rame, argento, acciaio inossidabile), per cui mettendo a contatto un metallo meno nobile e un metallo più nobile sarà il metallo meno nobile a corrodersi (fungendo da anodo) e la corrosione risulterà accelerata, invece il metallo più nobile rimarrà intatto a causa di un fenomeno di protezione.
I concetti che stanno alla base della corrosione per contatto galvanico di metalli possono essere estesi anche agli accoppiamenti di metalli e leghe con materiali da loro differenti, quali ossidi e solfuri, purché dotati di conducibilità elettronica (per esempio magnetite, solfuri di rame e ferro, grafite).
L'entità della corrosione dipende:
- dalla differenza di potenziale che si crea tra i due elementi, che è tanto più grande quanto più distanti sono gli elementi stessi nella scala dei potenziali standard (o scala galvanica);
- dalla quantità di ossigeno presente nell'ambiente;
- dal rapporto tra la superficie complessiva dei due metalli e quella del metallo meno nobile.
La nobiltà relativa dei diversi materiali metallici tiene conto di fattori cinetici, per cui non corrisponde ai valori termodinamici riportati nella serie elettrochimica dei potenziali di equilibrio di ossidoriduzione per le reazioni di ionizzazione dei vari metalli.
È necessario, infatti, conoscere anche i valori dei potenziali che i diversi materiali assumono una volta immersi in ambienti aggressivi "reali", stabilendo in questo modo delle serie galvaniche "pratiche", relative al comportamento dei vari materiali metallici qualora vengano accoppiati nei differenti ambienti in esame.
La nobiltà di un materiale metallico può infatti variare in un ampio intervallo di potenziale in dipendenza delle condizioni sia dell'ambiente (composizione, valore di pH, temperatura, presenza o assenza di condizioni di scambio termico, agitazione) sia del materiale metallico (passività a seguito della presenza di film superficiali protettivi o attività quando la superficie metallica è direttamente a contatto con il mezzo aggressivo).
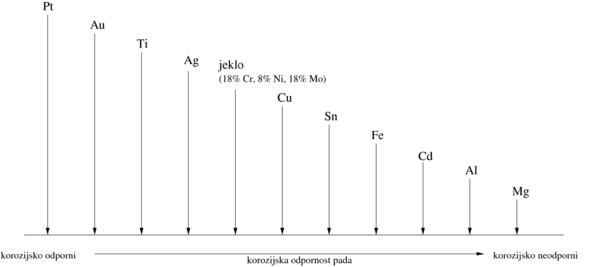
La realizzazione di accoppiamenti di materiali prossimi tra loro nelle serie galvaniche è quindi considerata favorevole, risultando questi materiali tra loro "galvanicamente compatibili", mentre è da evitare l'impiego di materiali tra loro lontani nella serie galvanica d'interesse.
Nel processo di corrosione per contatto, in qualche
Un esempio classico è quello della coppia Zn-Fe in acque naturali a temperatura elevata; lo zinco, metallo meno nobile e inizialmente anodico rispetto al ferro, a seguito della formazione di un film passivante stabile di ossido di zinco dotato di conducibilità elettronica, assumerà nel tempo un comportamento catodico rispetto al ferro.
Tra i fattori che regolano la corrosione per contatto va ricordata la conducibilità elettrica dell'ambiente aggressivo. Infatti, nei mezzi dotati di elevata conducibilità l'attacco è intenso e si fa sentire a distanze elevate, mentre in ambienti con alta resistività la corrosione risulta limitata alla zona anodica in prossimità della giunzione con l'area catodica. Per tale motivo questo tipo di corrosione risulta particolarmente grave in acque di mare ma non in acque dolci che hanno una conducibilità di almeno due ordini di grandezza più bassa.
Un altro fattore importante nella regolazione della corrosione galvanica è rappresentato dal rapporto tra le aree catodiche e quelle anodiche; le condizioni più sfavorevoli si realizzano quando l'area anodica è piccola rispetto a quella catodica, in quanto l'attacco corrosivo si concentra sull'area limitata. Un esempio tipico può essere l'impiego di elementi di giunzione in ferro (chiodi o viti) su strutture in rame o (come succede spesso nelle costruzioni idrauliche) bulloni in acciaio inox su tubazioni in acciaio al carbonio o in ghisa.
La prevenzione o il contenimento della corrosione per contatto possono essere realizzati evitando il contatto tra materiali di nobiltà molto diversa o isolando tra loro, ove possibile, materiali metallici differenti. Anche l'impiego di rivestimenti protettivi o di inibitori può ridurre il rischio di corrosione per contatto. Qualora sia impossibile evitare l'impiego di una coppia di materiali metallici tra loro non compatibili, si può ampliare la catena galvanica, introducendo un terzo metallo, meno nobile di quelli costituenti la coppia, agente quindi come anodo sacrificale.
Nobiltà dei metalli
[modifica | modifica wikitesto]
I metalli sono caratterizzati da una loro nobiltà,[12] che indica la maggiore o minor facilità dei materiali a cedere un certo numero di elettroni.
I metalli più nobili (ad esempio rame e argento) cedono più difficilmente gli elettroni che non i metalli meno nobili (ad esempio ferro e zinco).
Dal punto di vista puramente qualitativo, qui di seguito viene riportata la scala galvanica (riferita all'elettrodo a idrogeno) dei più comuni metalli e leghe (partendo dal meno nobile):
- Litio
- Sodio
- Magnesio
- Alluminio
- Manganese
- Zinco
- Cromo
- Ferro - (Acciaio al carbonio, Ghisa)
- Cadmio
- Nichel
- Stagno
- Piombo
- Rame
- Acciaio inossidabile
- Titanio
- Argento
- Mercurio
- Platino
- Oro
Comportamento elettrochimico dei metalli
[modifica | modifica wikitesto]Nei metalli, si distinguono due comportamenti elettrochimici:
- il comportamento elettrochimico attivo è caratteristico di quei metalli, come l'acciaio al carbonio, che ossidandosi danno origine a prodotti di corrosione insolubili (ad esempio ruggine), che una volta depositati sul materiale formano un film spugnoso e poco compatto, inadatto a impedire il processo anodico e pertanto a passivare il sottostante metallo;
- il comportamento elettrochimico passivo è caratteristico di quei metalli, come l'acciaio inossidabile, che ossidandosi danno origine a prodotti di corrosione insolubili che formano un sottile strato compatto e continuo capace di impedire il processo anodico e di conseguenza la corrosione del materiale sottostante.
Corrosione del ferro e delle sue leghe
[modifica | modifica wikitesto]
Nelle leghe ferrose, come gli acciai al carbonio e basso legati e le ghise, come vedremo in seguito, i prodotti insolubili che si formano per effetto della corrosione elettrochimica non risultano protettivi per il sottostante materiale e pertanto tali leghe hanno un comportamento elettrochimico attivo.
La condizione necessaria affinché si manifesti la corrosione elettrochimica del ferro, a temperatura normale, è che il manufatto si trovi in presenza di acqua e ossigeno.
In un metallo M isolato, immerso in una soluzione acquosa, avviene naturalmente la seguente reazione:
- M → Mn+ + ne-
Questo significa che il metallo M ha la tendenza a far passare in soluzione alcuni atomi disposti sulla sua superficie sotto forma di ioni Mn+.
Poiché gli ioni che passano in soluzione lasciano nel metallo i loro elettroni più esterni ne-, il metallo stesso si carica negativamente.
In questa situazione alcuni ioni Mn+ verranno attratti dal metallo e si ridepositeranno sulla sua superficie in forma metallica secondo la reazione:
- Mn+ + ne- → M
Quando le due reazioni raggiungono la stessa velocità si ha un equilibrio dinamico in cui il numero di atomi che lasciano il metallo è uguale al numero di ioni che si ridepositano su questo.
A questo punto Il metallo assumerà un determinato potenziale elettrico di equilibrio Eeq (potenziale di ossidoriduzione).
Qualora due metalli (o parti dello stesso metallo) a diverso potenziale vengono messi a contatto in presenza di un elettrolita, si forma una cella galvanica.
Il suddetto processo dipende dalla natura chimico-fisica del metallo e dal tipo di ambiente in cui è immerso. Sulla superficie dei manufatti in acciaio, a causa delle lavorazioni subite, vi sono sempre zone o punti che differiscono tra loro fisicamente o chimicamente e che pertanto hanno un diverso potenziale.
Tra due di questi punti, nonostante la differenza di potenziale (ΔE), non vi è però passaggio di corrente se l'ambiente è secco, anche in presenza di ossigeno, non potendosi realizzare un conduttore ionico.
Se invece sulla superficie del manufatto si deposita uno strato di acqua o un leggero velo di umidità, normalmente contenuta nell'atmosfera, tra i due punti con differenza di potenziale si vengono a costituire miriadi di minuscole pile, poiché:
- si genera un circuito ionico corrispondente al velo di acqua o umidità (conduttore di seconda specie)
- si genera un circuito elettronico corrispondente al metallo (conduttore di prima specie).
L'acqua infatti a causa del suo carattere anfotero è debolmente dissociata in ioni idrogeno H+ e ossidrili OH-:
- H2O → H+ + OH-
Pertanto, anche se l'acqua è purissima, presenta una piccola ma misurabile conducibilità elettrica. Per quanto sopra la corrosione nel ferro segue il seguente processo. Nella zona anodica, il ferro passa in soluzione cedendo all'acqua o al velo di umidità, lo ione Fe++ e liberando nel contempo degli elettroni:[13]
- Fe → Fe++ + 2e-
Gli elettroni liberati dagli atomi di ferro in corrispondenza dell'anodo, migrano attraverso il metallo (circuito elettronico) al catodo, dove reagiscono con gli ioni idrogeno H+ provenienti dal circuito ionico:[13]
- 2H+ + 2e- → H2
Questa reazione ha un duplice effetto: diminuisce la concentrazione di H+ rispetto a quella degli ioni ossidrili OH-, rendendo alcalina l'acqua a contatto col catodo; la formazione di bollicine di gas idrogeno ostacola l'avvicinamento di nuovi ioni idrogeno alla superficie del catodo, prevenendo la fuga di altri elettroni.
A questo punto interviene l'ossigeno disciolto nell'acqua (o nel velo di umidità) che, reagendo con il gas idrogeno, forma acqua e depolarizza il catodo:
- 2H2 + O2 → 2H2O
Nel contempo nella zona anodica gli ioni ossidrili provenienti dal catodo attraverso il circuito ionico, incontrano gli ioni ferrosi Fe++ che si diffondono dall'anodo nell'acqua o nel velo di umidità, formando idrato ferroso:
- 2Fe++ + 4OH- → 2Fe(OH)2
In presenza di sufficiente ossigeno nella zona anodica, lo ione ferroso viene ossidato a ione ferrico con formazione di ossido ferrico idrato (che costituisce chimicamente la ruggine),[10] poco solubile, che precipita sul metallo:
- 2Fe(OH)2 + ½O2 → Fe2O3.nH2O + H2O
Data la tendenza degli ioni ferrosi a diffondersi dall'anodo prima di combinarsi e formare la ruggine, questa depositatasi sulla superficie del manufatto in ferro, si presenta come un prodotto spugnoso con labile adesione sul metallo all'anodo.
Pertanto la sua azione protettiva (passivazione) non è sufficiente a inibire o arrestare il processo corrosivo come avviene invece nell'acciaio inossidabile (o nelle leghe di rame e di alluminio) per il quale i prodotti della corrosione, formando un film di ossidi continui e aderenti alla superficie del materiale, inibiscono il processo anodico in modo tale che la velocità di corrosione diventa del tutto trascurabile (comportamento elettrochimico passivo).
La continua perdita di metallo all'anodo può verificare profonde cavità e persino la perforazione dello stesso elemento in acciaio. Quanto su detto vale per l'azione dell'acqua e dell'ossigeno sulla corrosione dell'acciaio.
La conducibilità elettrica, dell'acqua, e pertanto la velocità di corrosione, aumenta in funzione della quantità di sali disciolti.
In atmosfera marina o in acqua di mare la conducibilità elettrica raggiunge valori molto superiori a quelli che si riscontrano nell'acqua chimicamente pura.
In questa situazione resta valido il meccanismo visto precedentemente, ma gli ioni ferrosi che si diffondono dall'anodo si combinano più facilmente con gli ioni cloro prodotti dalla dissociazione elettrolitica del cloruro di sodio nell'acqua o nel velo di umidità, formando cloruro ferroso:
- 4NaCl → 4Na+ + 4Cl-
- 2Fe++ + 4Cl- → 2FeCl2
Contemporaneamente nella zona catodica gli ioni sodio si combinano con gli ioni ossidrili (OH-) formando idrato di sodio:
- 4Na+ +4OH- → 4NaOH
La successiva reazione tra cloruro ferroso, idrato di sodio e l'ossigeno, presente nell'acqua o nel velo d'umidità, determina la formazione di ossido ferrico:
- 4FeCl2 + 8NaOH + O2 → 2Fe2O3 + 8NaCl + 4H2O
Poiché anche in questa caso sia il cloruro ferroso sia l'idrato sodico sono molto solubili, diffondendosi nel circuito ionico sia nella zona anodica sia catodica, la ruggine che deposita sulla superficie del materiale ferroso risulta ancora molto spugnosa e molto labile e pertanto non riesce a passivare il metallo.
Inoltre il processo di corrosione è ulteriormente facilitato dalla rigenerazione del cloruro di sodio.
Corrosione dei ferri d'armatura delle strutture in calcestruzzo armato
[modifica | modifica wikitesto]Anche l'armatura del calcestruzzo armato, pur essendo immersa nella matrice cementizia, può essere soggetta a fenomeni corrosivi. Questo avviene quando nel calcestruzzo, a seguito del processo di carbonatazione che si innesca per la diffusione dell'anidride carbonica all'interno della pasta cementizia, si ha una diminuzione del pH che determina l'ambiente ideale per l'innesco della corrosione dei ferri di armatura (per un calcestruzzo completamente carbonatato, il pH scende a circa 8,5).
Infatti esistono varie forme di idrossido di ferro che si genera a seguito dell'ossidazione del ferro metallico; in particolare in ambiente molto basico con pH > 11 (come si verifica nel calcestruzzo per effetto della presenza della calce), si forma un tipo di idrossido denominato lapidocrocite, il quale si presenta stabile, denso, compatto e aderente al sottostante supporto metallico creando una barriera impenetrabile all'ossigeno e all'umidità a tal punto che il processo di ossidazione avviene a una velocità trascurabile (ferro passivato).
In ambienti meno basici con pH < 11 (come si verifica nel calcestruzzo quando la calce è stata neutralizzata per effetto della carbonatazione) o, come vedremo in seguito, in ambienti contenenti cloruro, l'idrossido di ferro diviene poroso, permeabile all'ossigeno e all'umidità e quindi non più protettivo per il ferro sottostante (depassivazione del ferro) e pertanto si può innescare la corrosione.
In generale è possibile individuare due differenti periodi dell'attacco corrosivo:
- inizio che coincide con la costruzione dell'opera e si completa con la totale carbonatazione del copriferro o con il raggiungimento del limite di cloruri nel calcestruzzo (il pH <8,5)
- propagazione che inizia con l'innesco del fenomeno corrosivo che riduce le prestazioni strutturali fino a portare al non soddisfacimento degli stati limite di esercizio e/o ultimi.
Per effetto della corrosione i ferri d'armatura presentano sostanzialmente i seguenti fenomeni degradanti:
- la diminuzione della sezione resistente del tondino con conseguente riduzione del suo carico portante e della sua resistenza a fatica;
- la fessurazione del copriferro, che si forma in genere parallelamente alla direzione delle armature, con conseguente espulsione locale del copriferro (cricca o spalling se l'espulsione è angolare) o totale delaminazione (quando l'effetto di dirompente interessa più ferri vicini); questo avviene quando le tensioni che si generano nel calcestruzzo a causa dei fenomeni espansivi che accompagnano la formazione della ruggine, superano la resistenza a trazione del materiale. Naturalmente l'espulsione del copriferro provoca la completa esposizione dei ferri all'azione aggressiva dell'ambiente che viene pertanto accelerata.
- la riduzione di aderenza acciaio - calcestruzzo che può addirittura causare la perdita di ancoraggio con gravissime conseguenze.
- nel caso di acciai a elevato limite di snervamento (acciai armonici), cedimenti improvvisi per infragilimento da idrogeno.
In presenza di ioni cloro Cl-, la corrosione dei ferri di armatura può innescarsi anche con pH elevati (> 9), in questo caso si ha una corrosione localizzata detta corrosione per pitting (o vaiolatura). Questo tipo di corrosione può attaccare anche l'acciaio inox.
Protezione delle armature
[modifica | modifica wikitesto]La protezione delle armature d'acciaio contro la corrosione dipende dalla massa volumica del calcestruzzo, dalla qualità e dallo spessore del copriferro e dal grado di fessurazione del copriferro stesso.
La massa volumica e la qualità del copriferro si ottengono controllando il massimo rapporto acqua/cemento e il minimo contenuto di cemento.[14]
La fessurazione del copriferro può essere provocata da fenomeni come la variazione di temperatura, il ritiro, tanto plastico quanto igrometrico, lo scorrimento viscoso, e alle fessurazioni indotte nelle strutture in servizio da carichi dinamici e ciclici o da sollecitazioni termiche. Gli stessi prodotti espansivi della corrosione possono indurre fessurazioni aggiuntive del copriferro quando la corrosione viene innescata dalla penetrazione degli agenti aggressivi attraverso un calcestruzzo eccessivamente poroso.
Inoltre, nelle strutture in calcestruzzo prefabbricato, le fessure possono essere prodotte anche da urti meccanici o sollecitazioni flessionali indotte durante il trasporto, il sollevamento e il montaggio.
Un altro possibile mezzo di protezione e prevenzione dalla corrosione delle armature è quello di ricorrere a protezioni aggiuntive delle armature stesse, come l'utilizzo di tondini in acciaio zincato o acciaio inox.
Corrosione dei manufatti in ferro interrati
[modifica | modifica wikitesto]In assenza dell'azione dei batteri, la velocità di corrosione delle strutture interrate a matrice ferrosa (ghisa, acciaio) decresce al crescere della resistività dei terreni.
La resistività dipende da diversi fattori e in particolare da:
- struttura geologica
- dimensioni delle particelle
- porosità
- permeabilità
- contenuto di acqua.
Pertanto di norma i terreni che garantiscono un maggiore tenore di ossigeno, un idoneo contenuto di acqua (non asciutti ne troppo saturi) e un idoneo contenuto di sali elettroliti risultano a più alta corrosività.
La velocità di corrosione dipende inoltre da altri fattori quali:
- il pH: più acido è il terreno maggiore è l'azione corrosiva del terreno;
- il contenuto di cloruri e solfati, i quali esplicano un effetto depassivante e danno luogo a sali con il ferro con scarse proprietà protettive.
Corrosione dei manufatti in ghisa interrati
[modifica | modifica wikitesto]La ghisa, sia grigia sia sferoidale, insieme all'acciaio è il materiale più impiegato per la fabbricazione di tubi metallici.
Però mentre nell'acciaio il ferro passa in soluzione nell'elettrolita lasciando dei crateri visibili sulla superficie del metallo, nelle ghise i prodotti della corrosione della ferrite non si allontanano e restano frammisti alla grafite.
Questo fenomeno è noto come grafitizzazione.
I tubi grafitizzati mantengono spesso l'aspetto di quelli integri e una indicazione sull'estensione dell'attacco si può avere solo dopo la rimozione dei prodotti di corrosione.
Questi tubi danno un suono sordo quando sono percossi e possono essere facilmente incisi con una punta metallica.
In questa situazione il tubo può rompersi improvvisamente anche a basse pressioni, a seguito di sollecitazioni (quali ad esempio colpo d'ariete, traffico stradale o vibrazioni).
Una serie di prove effettuate negli Stati Uniti dal National Bureau of Standards (attualmente noto come National Institute of Standards and Technology o NIST) ha dimostrato che l'acciaio, la ghisa grigia e la ghisa sferoidale negli stessi terreni si corrodono pressoché con uguale velocità.[senza fonte]
Corrosione di materiali non metallici
[modifica | modifica wikitesto]Incidenti dovuti alla corrosione
[modifica | modifica wikitesto]
Di seguito sono riportati alcuni incidenti storici dovuti alla corrosione:
- 1967: crollo del ponte sospeso Silver Bridge tra Point Pleasant (Virginia Occidentale) e Kanauga (Ohio); causò la morte di 46 persone oltre a un grave danno economico di milioni di dollari;[15]
- 1988 incidente del volo Aloha Airlines 243: attribuito alla corrosione di una parte della fusoliera;[16][17]
- 1991: disastro della petroliera Kirki, che portò la morte di 120 persone;[18]
- 1992: la corrosione di una tubazione sotterranea contenente una miscela idrocarburica e il conseguente riversamento nelle condotte della rete fognaria provoca la morte di 230 persone a Guadalajara, in Messico.[19][20]
Pratiche contro la corrosione
[modifica | modifica wikitesto]Prove di corrosione
[modifica | modifica wikitesto]
Durante le prove di corrosione il materiale viene sottoposto a particolari condizioni che ne dovrebbero provocare la corrosione e a prova eseguita (o anche durante la prova) se ne misurano gli effetti.
Un esempio di prova di corrosione è la camera a nebbia salina: si tratta di un'apparecchiatura all'interno della quale il materiale che si vuole testare è sottoposto a un ambiente a elevata concentrazione salina; in questa maniera è possibile simulare il comportamento del materiale in ambienti marini.
Le camere cicliche di corrosione (o CCT, dall'inglese Cyclic Corrosion Test Chambers) permettono di simulare anche ambienti salini (come nel caso delle camere a nebbia salina), secchi o umidi ed è possibile modificare ciclicamente le condizioni all'interno della camera, in modo da simulare l'utilizzo del materiale in una molteplicità di possibili condizioni reali.
Tabelle di corrosione
[modifica | modifica wikitesto]Un modo immediato per prevedere se un materiale a contatto di una determinata sostanza è soggetto a corrosione consiste nell'utilizzo di "tabelle di corrosione",[21] le quali indicano alcune combinazioni materiale-elettrolita e per ciascuna di tali combinazioni indicano se il materiale è corrodibile o no.
Tali tabelle possono essere utilizzate in una prima fase della progettazione per scegliere il materiale più adatto per una determinata applicazione all'interno di una ristretta selezione di materiali.
Metodi di protezione dalla corrosione
[modifica | modifica wikitesto]
Per arrestare la corrosione si possono utilizzare una protezione di tipo passivo e/o di tipo attivo.
Nel primo caso la protezione serve a isolare la superficie del metallo dall'ambiente esterno mediante il suo rivestimento (previo accurata pulizia della stessa) con ad esempio:
- un film di pittura protettiva;
- manti protettivi a base di polietilene (secondo la UNI 9099), bitume (secondo la norma UNI 5256) e poliuretano, frequentemente usati come rivestimento esterno delle tubazioni in acciaio interrate; spesso si utilizzano anche nastri di polietilene autoadesivi applicati a freddo;[22]
- prodotti di ossidazione ottenuti ad esempio mediante l'ossidazione anodica, utilizzata per metalli come l'alluminio, il nichel o il cobalto; gli ossidi di tali materiali sono molto tenaci e aderenti allo strato superficiale e pertanto passivano il metallo;
- metalli meno nobili, quali lo zinco; in questo caso si parla della zincatura, usata per proteggere il ferro, effettuata immergendo il metallo, in un bagno fuso di zinco; poiché lo zinco è più riducente del ferro, anche se una parte della superficie ferrosa rimane scoperta, l'ossidazione procede sullo zinco (con formazione di ruggine bianca costituita prevalentemente da idrossido di zinco e in minima parte da ossido e carbonato) e il ferro rimane protetto fino a quando non è stato consumato tutto lo zinco;
- metalli più nobili, quali il cromo; in questo caso si parla di cromatura che viene utilizzata per proteggere i manufatti di ferro; il rivestimento della superficie del ferro avviene per lo più per via elettrolitica.

Le protezioni attive sono chiamate protezioni catodiche e sono utilizzate per eliminare i fenomeni di corrosione dei manufatti di ferro interrati.
Si possono distinguere due tipi di protezioni catodiche:
- a corrente impressa: consiste nell'applicare dall'esterno una fem contraria, ossia collegare il manufatto al polo negativo di un generatore esterno il cui polo positivo è a sua volta collegato a un elettrodo inerte (esempio grafite) interrato in prossimità del manufatto. L'umidità del terreno funge da elettrolita.
- ad anodo sacrificale o ad accoppiamento galvanico: consiste nel collegare direttamente il manufatto in ferro a un elettrodo interrato costituito da un metallo meno nobile (più riducente) del ferro stesso, quali lo zinco o il magnesio. Si viene a creare una cella galvanica in cui il ferro funge da catodo e l'elettrodo da anodo che di conseguenza si corrode preservando così l'integrità del manufatto in ferro fino a quando l'anodo non si consuma completamente.[10]
Monitoraggio della corrosione
[modifica | modifica wikitesto]Il monitoraggio della corrosione consiste nel misurare l'entità dei fenomeni corrosionistici durante l'utilizzo del materiale.
Ad esempio nel caso di sistemi di tubazioni si possono applicare dei sensori che forniscono una misura indiretta della velocità di corrosione, misurando ad esempio lo spessore o la resistività elettrica del materiale. In questa maniera è possibile pianificare eventuali attività di manutenzione o sostituzione dei tubi.
Note
[modifica | modifica wikitesto]- ^ Davis, p. 2.
- ^ Ullmann's, cap. 1.
- ^ a b c d e Ullmann's, cap. 2.
- ^ Pedeferri, p. 27.
- ^ a b Davis, p. 4.
- ^ http://www.euroviti.it/200mantec/PDFDOC/Sezione_06_3.pdf
- ^ (EN) IUPAC Gold Book, "contact corrosion"
- ^ Pedeferri, pp. 23-25.
- ^ IUPAC Gold Book, Non-uniform corrosion.
- ^ a b c The Columbia Encyclopedia.
- ^ L'acciaio inox a contatto con altri materiali metallici (PDF), su euro-inox.org. URL consultato il 2 aprile 2014 (archiviato dall'url originale il 24 settembre 2015).
- ^ Esistono due definizioni di "metallo nobile": un metallo è detto nobile se appartiene al gruppo 11 della tavola periodica oppure se è posto in cima alla scala di nobiltà dei metalli (definita in termini di facilità alla corrosione).
- ^ a b Concise Encyclopedia of Science and Technology.
- ^ vedere UNI EN 206-1:2001 e UNI 11104:2004
- ^ Davis, p. 3.
- ^ Aloha Incident - Corrosion A-H - NACE International Archiviato il 4 maggio 2011 in Internet Archive.
- ^ Roberge, pp. 3-4.
- ^ Roberge, p. 4.
- ^ Corriere della Sera, Nel cerchio della morte di Guadalajara
- ^ Roberge, p. 3.
- ^ Copia archiviata (PDF), su oleodinamicatoscana.it. URL consultato il 6 giugno 2011 (archiviato dall'url originale il 27 febbraio 2012).
- ^ Questo tipo di rivestimento esterno è molto utilizzato in cantiere, dove viene applicato a mano, per proteggere esternamente le zone di giunzione saldate, normalmente sprovviste di rivestimento esterno per circa 10+10 cm a cavallo della saldatura, oppure nel rivestite i pezzi speciali in acciaio(curve, T, ecc.) costruiti in cantiere, al fine di garantire la continuità dielettrica esterna all'intera condotta interrata; raramente vengono applicati in stabilimento mediante macchina avvolgitrice. Normalmente si procede nel seguente modo a) asportazione di ogni scoria, impurità ecc. dalla zona da rivestire mediante spazzole o attrezzi analoghi; b) applicazione a pennello del primer bituminoso; c) avvolgimento a spirale di nastri adesivi di protezione dalla corrosione (inner tape), normalmente di colore nero, con una sovrapposizione minima di 25 mm tra gli avvolgimenti contigui e di almeno 100 mm sul manto protettivo esterno esistente; d) avvolgimento a spirale di nastri adesivi di protezione meccanica (outer tape), normalmente di colore bianco, procedendo nel medesimo modo del punto c) ma sovrapponendolo al rivestimento esterno esistente per almeno 50 mm.
Bibliografia
[modifica | modifica wikitesto]- Pietro Pedeferri, Corrosione e protezione dei materiali metallici, 2ª ed., CittàStudi, 1978, ISBN 88-251-0130-9.
- Luciano Lazzari, Pedeferri Pietro, Ormellese Marco, Protezione catodica, Polipress, 2006, ISBN 88-7398-028-7.
- Michele Cioffi, La pitturazione delle costruzioni di acciaio, CISIA, 1973.
- Adriano Sacco, Chimica, Adriatica Editrice.
- Pietro Pedeferri, L. Bertolini, La corrosione nel calcestruzzo e negli ambienti naturali, McGraw-Hill.
- (EN) Hubert Gräfen, Elmar-Manfred Horn, Hartmut Schlecker, Helmut Schindler, Ullmann's Encyclopedia of Industrial Chemistry, "Corrosion", 7ª ed., Wiley-VCH, 2004, DOI:10.1002/14356007.b01_08.
- (EN) Joseph R. Davis, Corrosion: understanding the basics, ASM International, 2000, ISBN 0-87170-641-5.
- (EN) Pierre R. Roberge, Handbook of corrosion engineering, McGraw-Hill Professional, 2000, ISBN 0-07-076516-2.
- (EN) M. McNaught, A. Wilkinson, IUPAC. Compendium of Chemical Terminology ("Gold Book"), 2ª ed., Oxford, Blackwell Scientific Publications, 1997, DOI:10.1351/goldbook, ISBN 0-9678550-9-8.
- (EN) The Columbia Encyclopedia, New York, Columbia University Press, 2008.
- (EN) Concise Encyclopedia of Science and Technology, New York, McGraw-Hill, 2006.
Voci correlate
[modifica | modifica wikitesto]- Biocorrosione
- Erosione
- Inibitore di corrosione
- Passivabilità
- Potenziale standard di riduzione
- Ruggine
- Tensocorrosione
- Inibitore volatile di corrosione
- Sostanza corrosiva
- Corrosione del vetro
Altri progetti
[modifica | modifica wikitesto]Wikizionario contiene il lemma di dizionario «corrosione»
Wikimedia Commons contiene immagini o altri file sulla corrosione
Collegamenti esterni
[modifica | modifica wikitesto]- (EN) corrosion, su Enciclopedia Britannica, Encyclopædia Britannica, Inc.
- Modi di guasto per corrosione., su materials.open.ac.uk.
- Tabella qualitativa di resistenza alla corrosione di alcuni materiali., su engineeringtoolbox.com.
- Elettrochimica della corrosione., su electrochem.cwru.edu. URL consultato il 16 novembre 2008 (archiviato dall'url originale il 22 ottobre 2008).
- Corrosione dell'acciaio., su azom.com.
- La corrosione dell'acciaio, su infobuilddossier.it (archiviato dall'url originale il 28 novembre 2011).
- Corrosione (PDF) [collegamento interrotto], su dim.unipd.it.
- Principali forme di corrosione (PDF), su unibg.it.
- (EN) Electrochemistry of corrosion, su electrochem.cwru.edu. URL consultato il 21 maggio 2011 (archiviato dall'url originale il 3 maggio 2009).
- (EN) Kinetics of Aqueous Corrosion, su doitpoms.ac.uk.
Controllo di autorità | Thesaurus BNCF 37941 · LCCN (EN) sh85033050 · GND (DE) 4032518-0 · BNF (FR) cb11975888z (data) · J9U (EN, HE) 987007567881705171 · NDL (EN, JA) 00563793 |
---|