Indice
-
Inizio
-
1 Ferro meteoritico
-
2 Medio Oriente
-
3 India
-
4 Cina
-
5 Giappone
-
6 Europa
-
6.1 La ferriera alla genovese
-
6.2 L'acciaio a pacchetto
-
6.3 I primi forni da ghisa in Europa
-
6.4 Processi di affinamento
-
6.5 L'acciaio Bulat
-
6.6 L'acciaio cementato
-
6.7 Sviluppo delle fonderie alimentate idraulicamente
-
6.8 L'invenzione del carbon coke
-
6.9 Abraham Darby e i suoi successori
-
6.10 La reinvenzione dell'acciaio al crogiolo
-
6.11 Nuovi processi di forgiatura
-
6.12 Vento caldo
-
6.13 Il forno Martin-Siemens
-
6.14 L'invenzione del convertitore
-
6.15 L'acciaio inox
-
6.16 I convertitori a ossigeno
-
-
7 Note
-
8 Bibliografia
-
9 Voci correlate
-
10 Altri progetti
-
11 Collegamenti esterni
Storia della siderurgia
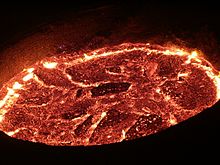

Per poter comprendere la storia della siderurgia, è necessario avere presente le seguenti definizioni:
- Ferro: attualmente con tale termine si intende l'elemento chimico Fe o ferro puro (il quale fonde a circa 1538 °C,[1] ha scarsissime proprietà tecnologiche e presenta un'elevata facilità ad ossidarsi); ma nell'antichità e fino al XIX secolo la parola identificava quel particolare tipo di ferro che era malleabile a caldo e non prendeva la tempra.
- Ferro battuto: lega ferro-carbonio a bassissimo tenore di carbonio, malleabile, di cui sopra.
- Acciaio: lega ferro-carbonio, con contenuto ponderale[2] di carbonio fino al 2,11%. Nell'antichità e fino al XVIII secolo si pensava fosse un particolare tipo di ferro cui mancava qualcosa. Era ottenuto in forni chiusi o per parziale aggiunta di ghisa al ferro in crogioli: la sua caratteristica era la "fragilità" cioè la poca resistenza alla frattura a freddo e la sua temprabilità a caldo.
- Ghisa: lega ferro-carbonio, con contenuto ponderale di carbonio superiore al 2,11%. È troppo fragile per essere lavorata per forgiatura. La ghisa in getti si otteneva da forni chiusi di particolare fattura, insufflati con macchine mosse da ruote idrauliche a partire dal XII secolo in Svezia, Germania e Nord Italia. Dalla ghisa si otteneva ferro o acciaio nelle fucine, anch'esse alimentate con mantici idraulici.[3]
Ferro meteoritico
[modifica | modifica wikitesto]
La fabbricazione di oggetti di uso comune a partire da ferro meteorico viene fatta risalire al III secolo a.C.[4]
A causa del fatto che le meteoriti cadono dal cielo, alcuni linguisti hanno ipotizzato che la parola inglese iron (inglese antico:i-sern), che ha parenti in molte lingue nordiche ed occidentali, derivi dall'etrusco aisar, che significa "Gli Dei".[5] Anche se così non fosse, la parola è stata probabilmente importata nelle lingue pre-proto-germaniche, da quelle celtiche o italiche.[6][7] Krahe ne compara forme in irlandese antico, illirico, veneto e messapico.[8] L'origine meteoritica del ferro nel suo primo utilizzo da parte degli uomini[9] viene anche citato nel Corano:
«Invero inviammo i Nostri messaggeri con prove inequivocabili, e facemmo scendere con loro la Scrittura e la Bilancia, affinché gli uomini osservassero l'equità. Facemmo scendere il ferro, strumento terribile e utile per gli uomini, affinché Allah riconosca chi sostiene Lui e i Suoi messaggeri in ciò che è invisibile. Allah è forte, eccelso»
Il ferro aveva un uso limitato prima che fosse possibile fonderlo. I primi segni dell'uso del ferro vengono dall'antico Egitto e dai Sumeri, dove attorno al 4000 a.C. venivano prodotti piccoli oggetti di ferro meteoritico come ornamenti o come punte delle lance.[10] Tuttavia, il loro uso sembra fosse cerimoniale, e il ferro era un metallo costoso: infatti nel 1600 a.C. il ferro aveva un costo cinque volte maggiore rispetto all'oro e quattro volte maggiore dell'argento. Alcuni meteoriti (dette "sideriti" o "meteoriti ferrose") contengono una lega di ferro e nichel,[11] e il ferro recuperato dalle cadute di meteoriti ha permesso agli antichi di fabbricare pochi piccoli manufatti in ferro.
Nell'Anatolia, il ferro fuso era usato a volte per armi ornamentali: una daga con lama di ferro e elsa di bronzo è stata ritrovata da una tomba ittita datata 2500 a.C. Anche il Faraone egizio Tutankhamon che morì nel 1323 a.C. fu sepolto assieme a una daga di ferro con elsa d'oro. Furono anche ritrovati negli scavi di Ugarit un'antica spada egizia che portava il nome del faraone Merneptah e un'ascia da battaglia con lama di ferro e manico di bronzo decorato con oro.[12] I primi ittiti barattavano con gli assiri un peso di ferro contro 40 di argento. Il ferro meteoritico veniva usato per ornare gli strumenti nell'America settentrionale precolombiana. A partire dall'anno 1000, il popolo groenlandese di Thule cominciò a fabbricare arpioni e altri strumenti affilati da pezzi del meteorite di Capo York.[13][14] Questi manufatti furono anche usati come bene di scambio con le altre popolazioni artiche: strumenti fatti dal meteorite di Capo York sono stati trovati in siti archeologici distanti oltre 1.600 km. Quando l'esploratore statunitense Robert Edwin Peary portò il più grande frammento del meteorite all'American museum of natural history a New York nel 1897, pesava ancora oltre 33 tonnellate.[15]
Medio Oriente
[modifica | modifica wikitesto]Preistoria ed antichità
[modifica | modifica wikitesto]
Le prime prove di uso del ferro vengono dai Sumeri e dagli Egiziani, che già 4.000 anni prima di Cristo lo usavano per la manifattura di piccoli oggetti, come punte di lancia e gioielli, ricavati dal ferro recuperato dai meteoriti.
Al periodo che va dal 3000 a.C. al 2000 a.C. risalgono molti oggetti in ferro battuto (distinguibili dagli oggetti in ferro meteorico per la mancanza di nichel nella lega), ritrovati in Mesopotamia, Anatolia ed Egitto; il loro uso sembra essere cerimoniale: il ferro infatti era un metallo costoso, anche più dell'oro. Nell'Iliade la maggior parte delle armi e delle armature menzionate sono di bronzo,[16][17][18] e i masselli di ferro sono usati per commerciare. Nel 1500 a.C. circa un numero sempre più grande di oggetti di ferro appare in Mesopotamia, in Anatolia e in Egitto.[19]
Ipotesi sull'ascesa del ferro sul bronzo
[modifica | modifica wikitesto]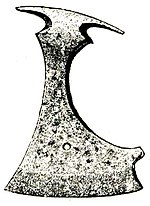
Tra il XII secolo a.C. e il X secolo a.C. il ferro rimpiazzò il bronzo nella produzione di attrezzi e di armi nel Mediterraneo orientale (il Levante, Cipro, la Grecia, Creta, l'Anatolia e l'Egitto).[20][21] Anche se gli oggetti di ferro sono conosciuti dall'età del Bronzo lungo il mediterraneo orientale, essi sono ritrovati solo sporadicamente e sono statisticamente insignificanti comparati alla quantità di oggetti in bronzo di questo stesso periodo.[22] Questa transizione, avvenuta in diverse epoche nelle diverse regioni del pianeta, segna l'inizio dello stadio di civiltà noto come "età del ferro". Una ormai screditata spiegazione dell'ascesa del ferro attribuiva agli Ittiti dell'Anatolia il monopolio della tecnologia del ferro durante la tarda età del bronzo.[23]. Questa teoria non è più insegnata nei programmi scolastici,[23] perché priva di riscontri storici e archeologici. Anche se sono stati ritrovati alcuni oggetti di ferro dell'Anatolia dell'età del bronzo, il loro numero è comparabile a quello degli oggetti di ferro trovati in Egitto o in altri luoghi dello stesso periodo, e solo una piccola parte di essi sono armi.[22] In particolare nell'Asia Minore i regni ittiti all'interno dell'Anatolia si trovarono tagliati fuori dal commercio dello stagno: per tale motivo la tribù dei Calibi sviluppò la tecnica di carburazione del ferro con carbonella per sostituire il bronzo. Verso il XIII secolo a.C. si sviluppò nei Balcani la cultura cittadina degli Illiri, che si impadronì di tutto lo stagno proveniente dalle miniere della Boemia, bloccando il rifornimento di questo metallo nel mar Egeo. Questo provocò una grave crisi economica e di conseguenza le invasioni in Egitto dei popoli del Mare e la guerra di Troia, ed infine l'avvento dell'età del ferro nel Mediterraneo. Alcune fonti ipotizzano che il ferro fu inizialmente ottenuto utilizzando gli stessi forni che servivano per la raffinazione del rame. Una teoria più recente dell'ascesa del ferro riguarda il collasso degli imperi che alla fine della tarda età del bronzo mandò in frantumi le vie del commercio, necessarie per la produzione del bronzo.[23] La disponibilità del rame e ancor più dello stagno era scarsa, per cui si richiedeva il trasporto di queste materie prime per lunghe distanze. Si pensa che all'inizio dell'età del ferro il trasporto di queste materie prime non fosse sufficiente a colmare la richiesta da parte di coloro che lavoravano i metalli. Da qui sarebbe potuto nascere l'utilizzo del minerale di ferro, che è più abbondante in natura rispetto ai minerali di rame e stagno. Quindi l'ascesa del ferro potrebbe essere stata il risultato di una necessità, causata principalmente dalla mancanza di stagno. Anche in questo caso mancano le prove archeologiche che dimostrino in particolare una mancanza di rame o stagno nella prima età del ferro.[23] Gli oggetti in bronzo sono ancora abbondanti e questi oggetti hanno la stessa percentuale di stagno di quelli della fine dell'età del bronzo.
La Mesopotamia era già in piena età del ferro nel 900 a.C., l'Europa centrale nell'800 a.C. L'Egitto, d'altra parte, non sperimentò una così rapida transizione dall'età del bronzo a quella del ferro: anche se i fabbri egizi producevano oggetti di ferro, il bronzo rimase largamente diffuso fino alla conquista dell'Egitto da parte degli Assiri nel 663 a.C.
Il processo di carburazione
[modifica | modifica wikitesto]Contemporanea alla transizione dal bronzo al ferro fu la scoperta della carburazione (o carbocementazione), ovvero il processo per arricchire superficialmente di carbonio il ferro malleabile.
Il ferro era ottenuto dal suo minerale in forni alimentati con carbone di legna la cui combustione era favorita dall'insufflaggio di aria forzata prodotta da mantici. Il monossido di carbonio prodotto dal carbone riduceva gli ossidi del ferro in ferro metallico; questo si raccoglieva in forma di massa spugnosa o fiore, i cui pori contenevano carbonio e/o carburi (provenienti dalle ceneri) e scorie. Il fiore doveva poi essere riscaldato nuovamente per poterlo battere ed espellerne le scorie ancora imprigionate in esso (per lo più frammenti di carbone e o minerale e parte del carbonio). Se ne otteneva ferro malleabile non temprabile e una parte di acciaio che l'occhio del pratico sapeva riconoscere. Le genti del Medio Oriente scoprirono che un ferro molto più duro poteva essere creato riscaldandolo a lungo in un involucro di polvere di carbone, trasformando lo strato superficiale del materiale in acciaio, poi temprabile.
Le spade Damasco (acciaio al crogiolo)
[modifica | modifica wikitesto]
Poco dopo l'anno mille, la tecnica indiana del Wootz arriva in Medio Oriente, che fino ad allora aveva importato acciaio a pacchetto dall'Europa, dove viene ulteriormente raffinata e dà origine all'acciaio Damasco, estremamente resistente e flessibile, con cui furono forgiate le spade che affrontarono i crociati europei. La qualità di queste armi era tanto alta che si diceva che una spada fatta di acciaio Damasco potesse tagliare la roccia, e venire arrotolata attorno a un uomo per poi tornare dritta come prima, e non perdesse mai il filo. Con ogni probabilità la tecnica del Wootz venne raffinata in modo da far assorbire il carbonio soprattutto ai bordi della spada, mantenendo la sua anima centrale relativamente dolce. In questo modo si otteneva una spada flessibile e che sopportava gli urti senza rompersi, ma al tempo stesso dalla lama molto dura e mantenente un filo tagliente per molto tempo (cosa che in Europa, fino al X secolo, era ottenuta montando a parte i due fili d'acciaio molto duro sulla lama, già ripiegata più volte e lavorata fino alla forma definitiva).[24] Le variazioni nel tenore di carbonio fra il filo e il centro della spada creavano in superficie un bel disegno ondulato, dal cui l'aggettivo damascato. Non sono pervenuti documenti o testimonianze sul modo di ottenere l'acciaio Damasco;[25] per un certo tempo si ritenne che l'acciaio Damasco non fosse altro che un tipo di acciaio a pacchetto, che in certe condizioni può esibire delle venature superficiali, ma un confronto con i manufatti in acciaio Damasco superstiti evidenziano differenze sostanziali, sebbene a volte anche l'acciaio Damasco mostri tracce di pacchettatura.
India
[modifica | modifica wikitesto]Siti archeologici in India, come quello di Malhar, di Dadupur, di Raja Nala Ka Tila e di Lahuradewa nell'attuale Uttar Pradesh mostrano utilizzi del ferro nel periodo tra il 1800 a.C. e il 1200 a.C.[26]
I primi oggetti di ferro trovati in India possono essere datati al 1400 a.C. impiegando il metodo di datazione del carbonio radioattivo. Punte, coltelli, daghe, punte di freccia, ciotole, cucchiai, padelle, asce, ceselli, pinze, cerniere delle porte, ecc. che vanno dal 600 a.C. al 200 a.C. sono state trovate in diversi siti archeologici indiani.[27] Alcuni studiosi credono che all'inizio del XIII secolo a.C., la produzione di ferro fosse praticata su larga scala in India, suggerendo che la data di scoperta della tecnologia possa essere anticipata.[26] Nell'India meridionale (oggi chiamata Mysore) si hanno rinvenimenti di acciaio la cui datazione va dall'XI secolo a.C. al XII secolo a.C.[28]
L'inizio del I millennio a.C. vide molti sviluppi nella metallurgia del ferro in India. Gli avanzamenti tecnologici e la padronanza della metallurgia fu raggiunta durante questo periodo di colonizzazione pacifica.[28] Gli anni a venire videro diverse trasformazione delle tecniche metallurgiche durante il periodo politicamente stabile dell'impero Maurya.[29]
Lo storico greco Erodoto diede la prima testimonianza scritta occidentale sull'uso del ferro in India.[27] Nei testi religiosi indiani (chiamati Upaniṣad) sono riportati dei riferimenti all'industria tessile, ceramica e metallurgica.[30]
L'acciaio wootz
[modifica | modifica wikitesto]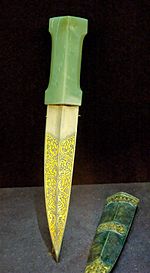
Il primo metodo per produrre acciaio propriamente detto (ovvero acciaio di alta qualità), è stato il "wootz", simile al moderno metodo a crogiolo, usato nell'India meridionale almeno dal 300 d.C. (ma alcuni lo fanno risalire al 200 a.C.); wootz è la versione anglicizzata del nome indù ukku o urukku che significa “acciaio”. Veniva preparato in crogioli chiusi sigillati, che contenevano minerale di ferro ad alta purezza, carbone e vetro. I crogioli venivano poi messi alla fiamma e riscaldati fino ad avere la fusione del miscuglio, per cui il ferro si arricchiva di carbonio, e il vetro assorbiva le impurità man mano che fondeva, galleggiando sulla superficie.[31] Il risultato era un acciaio ad alto tenore di carbonio e di elevata purezza, chiamato poi acciaio di Damasco. Questa tecnica si diffuse molto lentamente, arrivando nei paesi confinanti (gli odierni Turkmenistan e Uzbekistan) solo nel 900 d.C. circa. La fornace per la produzione degli acciai di Damasco era una fornace a vento, che utilizzava i venti dei monsoni per il suo funzionamento.[31]
L'acciaio di Damasco è famoso anche per la sua resistenza e la capacità di mantenere il filo. Era una lega complessa, che aveva il ferro come componente principale. Studi recenti hanno suggerito che nanotubi di carbonio (prodotti in maniera inconsapevole durante il processo) fossero inclusi nella sua struttura, il che potrebbe spiegare le sue caratteristiche meccaniche.[32]
Catene di ferro furono utilizzate dagli indiani per la costruzione di ponti sospesi prima del IV secolo.[33]
La Colonna di Ferro che si erge nel complesso di Qutba Delhi, capitale dell'India è una delle più antiche curiosità metallurgiche del mondo. Il pilastro (alto quasi sette metri e pesante oltre sei tonnellate) fu eretto da Chandragupta II Vikramaditya.[34] Il pilastro ha un contenuto di ferro del 98%, ma ha resistito alla corrosione per gli ultimi 1.600 anni, contrastando le condizioni meteorologiche avverse grazie al suo elevato contenuto di fosforo. La tecnica indiana mise molto tempo a giungere in Europa. A partire dal XVII secolo gli olandesi portavano l'acciaio di Damasco dall'India del sud all'Europa, dove in seguito si avviò la sua produzione in larga scala, con il nome di tecnica del crogiolo.[35]
Will Durant scrisse nel suo The Story of Civilization I: Our Oriental Heritage ("La storia della civiltà I: La nostra eredità Orientale"):
«Qualcosa è stato detto sull'eccellenza chimica della ghisa nell'India antica, e sull'elevato sviluppo industriale del periodo Gupta, quando l'India veniva vista, perfino dalla Roma imperiale, come la più abile delle nazioni in diversi tipi di industria chimica, come quella dei coloranti, della concia, della fabbricazione del sapone, del vetro e del cemento... Dal sesto secolo gli Hindu erano molto più avanti dell'Europa nell'industria chimica; erano maestri della calcinazione, della distillazione, della sublimazione, della cottura a vapore, della fissazione, della produzione della luce senza calore, la preparazione di anestetici e polveri soporifere e della preparazione di sali metallici, composti e leghe. La tempra dell'acciaio in India fu portata a una perfezione sconosciuta in Europa fino ai nostri tempi; si dice che il Raja Puru abbia scelto, come dono speciale da Alessandro Magno non oro o argento, ma 30 libbre di acciaio. I musulmani portarono molta di questa scienza e industria Hindu nel Vicino Oriente e in Europa; i segreti della fabbricazione delle lame di "Damasco", per esempio, vennero presi dagli arabi dai Persiani, e questi ultimi li presero dall'India.»
Cina
[modifica | modifica wikitesto]I primi sviluppi in Cina
[modifica | modifica wikitesto]
Anche in Cina il primo ferro usato fu di origine meteorica. Manufatti di ferro battuto compaiono in siti archeologici datati attorno all'VIII secolo a.C. nel nord-ovest, vicino a Xinjiang. Questi pezzi sono stati fatti con le stesse tecniche in uso nel Medio Oriente ed in Europa. La produzione di acciaio, benché presente, soprattutto per la produzione di armi, era limitata. Negli ultimi anni della dinastia Zhou (attorno all'anno 550 a.C.), nello Stato meridionale di Wu si sviluppò un'avanzata tecnologia basata su forni a torre, rastremati alla base, in grado di produrre ghisa in grandi quantità.[36][37][38] Alla loro temperatura di esercizio, anche più di 1.200 °C il ferro si combina con il 4,3% di carbonio e fonde ed è colato in stampi. Scaldando minerali di ferro con carbone a 1.200-1.300 °C si forma ghisa liquida, che è una lega di ferro al 96,5% e carbonio al 3,5%. Questa lega è troppo fragile per essere lavorata (in particolare è inadatta per impieghi da impatto), a meno che non venga decarburata per rimuovere la maggior parte del carbonio. La ghisa quindi veniva colata in stampi e decarburata fino allo stato di ferro dolce, arroventandola in focolari aperti per diversi giorni.
In Cina, questi metodi di lavorazione del ferro si diffusero a nord, e nel 300 a.C. il ferro era il materiale maggiormente impiegato per la produzione di attrezzi e di armi. Una grande tomba nella provincia di Hebei (datata all'inizio del III secolo a.C.) contiene diversi soldati sepolti con le loro armi ed altro equipaggiamento. I manufatti recuperati da questa tomba sono fatti di ferro battuto, di ghisa, ghisa malleabile e acciaio temprato, con alcune armi di bronzo, probabilmente ornamentali. Il ferro rimase un prodotto poco pregiato, usato dai contadini per secoli e non interessò le classi nobiliari fino alla Dinastia Han (202 a.C. – 220 d.C.), durante la quale la lavorazione del ferro cinese (più propriamente della ghisa) raggiunse una scala ed una sofisticazione elevatissime. Nel primo secolo, il governo Han fece diventare la lavorazione del ferro un monopolio di Stato e fece costruire una serie di grandi forni nella provincia di Henan, ognuno capace di produrre diverse tonnellate di ghisa al giorno. In questa epoca, i metallurgi cinesi scoprirono come impastare la ghisa grezza fusa rimescolandola all'aria aperta fino a che non avesse perso il carbonio e non fosse divenuta ferro malleabile (in lingua cinese il processo veniva chiamato chao, letteralmente saltato e fritto). Nel I secolo a.C., i metallurgi cinesi scoprirono che il ferro e la ghisa potevano essere saldati assieme per formare una lega con contenuto intermedio di carbonio, che era acciaio.[39][40][41] Secondo una leggenda, la spada di Liu Bang, il primo imperatore Han, fu creata con questa tecnica[senza fonte]. Alcuni testi del tempo menzionano l'armonizzazione del duro e del morbido nel contesto della lavorazione del ferro; la frase potrebbe riferirsi a questo processo. Inoltre, la città antica di Wan (Nanyang) del periodo Han precedente era un grosso centro manifatturiero di ferro e acciaio.[42] Assieme ai loro metodi originali per forgiare l'acciaio, i cinesi hanno anche adottato i metodi di produzione per creare l'acciaio Damasco, un'idea importata dall'India alla Cina nel V secolo d.C.[43]
La tecnologia cinese degli altiforni (o acciaio al crogiolo) e del pudellaggio fu ripresa in Europa nel tardo Medioevo.
I mantici ad acqua cinesi
[modifica | modifica wikitesto]
I cinesi durante l'antica Dinastia Han furono anche i primi ad applicare l'energia idraulica (da un mulino ad acqua) per fare funzionare i mantici di una fornace. Questo fu annotato nell'anno 31 d.C., come innovazione dell'ingegnere Du Shi, del prefetto di Nanyang.[44] Dopo Du Shi, i cinesi continuarono a utilizzare l'energia dell'acqua per muovere i mantici delle fornaci. Nel testo del Wu Chang Ji del V secolo il suo autore Pi Ling scrisse che un lago artificiale fu progettato e costruito nel periodo del regno di Yuan-Jia (424–429) per il solo scopo di alimentare le ruote dei mulini aiutando i processi di fusione e stampaggio dell'industria del ferro cinese.[45] Il testo del V secolo Shui Jing Zhu menziona l'uso dell'acqua corrente di fiume per alimentare i mulini, come ne parla il testo geografico dello Yuan.he Jun Xian Tu Chi della Dinastia Tang, scritto nell'814 d.C.[46]
Ci sono prove che la produzione dell'acciaio nell'XI secolo nella Cina dei Song avvenisse usando due tecniche: un medodo "berganesque", che produceva un acciaio inferiore e disomogeneo e un precursore al moderno processo Bessemer, che utilizzava una decarburizzazione parziale attraverso forgiature ripetute sotto un soffio freddo.[47] Nell'XI secolo ci fu anche una grossa deforestazione in Cina, a causa delle richieste di carbone dell'industria siderurgica.[48] In questo periodo i cinesi scoprirono come usare il carbon coke al posto del carbone vegetale.[48] L'introduzione del carbone minerale al posto del carbone vegetale si ebbe poi in Europa nel XVII secolo.
Anche se Du Shi fu il primo a utilizzare l'energia idraulica per alimentare i mantici nella metallurgia, la prima illustrazione disegnata ed illustrata di questa alimentazione idraulica risale al 1313, nel testo dell'era della Dinastia Yuan chiamato Nong Shu.[45] Il testo fu scritto da Wang Zhen (1290-1333 d.C.), che così spiegò i metodi usati per l'altoforno con mantici alimentati ad acqua nei periodi precedenti la sua era del XIV secolo:
«"In accordo con gli studi moderni (+1313!), i mantici con sacco in cuoio (wei nang) erano usati ai vecchi tempi, ma ora vengono usati sempre dei ventagli in legno. Il design è il seguente. Viene scelto un luogo vicino a un forte torrente, e un palo viene innalzato verticalmente in una struttura con due ruote orizzontali in modo da avere quella più in basso spinta dalla forza dell'acqua. La più alta è collegata con una cinghia a una ruota (più piccola) davanti ad essa, la quale ha un manico eccentrico (letteralmente un ingranaggio oscillante). Poi vi è un blocco, che segue la rotazione (della ruota principale), con un ingranaggio collegato al manico eccentrico che tira e spinge il rullo oscillante, le leve a destra e a sinistra del quale assicurano la trasmissione del moto all'ingranaggio del pistone. Quindi questo viene spinto avanti e indietro, azionando i mantici della fornace molto più velocemente di quanto sarebbe possibile con la forza umana.[49]»
«Viene usato anche un altro metodo. Alla fine del pistone in legno, lungo circa 3 piedi che viene fuori dalla parte frontale dei mantici, c'è un pezzo incurvato di legno con la forma della luna crescente, e (tutto) questo è sospeso in alto con una corda come quella di un'altalena. Poi, davanti ai mantici, ci sono (molle di) bambù collegate ad essi dalle corde; questo controlla il movimento del ventaglio dei mantici. Poi, seguendo la rotazione della ruota (verticale) del mulino, il manico collegato all'asse principale schiaccia e preme la tavola incurvata (collegata al pistone) che corrispondentemente si muove indietro (letteralmente "in dentro"). Quando il manico è finalmente disceso il bambù (le molle) agisce sui mantici e li riportano nella posizione iniziale. In maniera simile, usando un solo asse principale, è possibile attuare diversi mantici (con estensioni sull'asse), con lo stesso principio dei martelli a caduta (shui tui). Questo è anche molto conveniente e veloce...[49]»
Giappone
[modifica | modifica wikitesto]Spade da samurai
[modifica | modifica wikitesto]
In Giappone i costruttori di spade furono gelosi custodi delle loro tecniche di fabbricazione dell'acciaio usato per le spade da samurai.
La tecnica era (ed è ancora) simile a quella utilizzata per l'acciaio a pacchetto, ma con alcune differenze sostanziali: la lama veniva realizzata dividendo la battitura a strati prima su una parte esterna di acciaio più duro, destinata a divenire la parte esterna e il filo della lama, nella quale in seguito veniva parzialmente inserita una barra di acciaio più morbido che ne costituiva l'anima flessibile. La katana assumeva in tal modo, dopo la forgiatura, la tempra e la pulizia, un'estrema affilatura ed un'estrema flessibilità.
Europa
[modifica | modifica wikitesto]La ferriera alla genovese
[modifica | modifica wikitesto]
Nella seconda metà del XIV secolo fece la sua comparsa nella Repubblica di Genova un nuovo modo di produrre il ferro in un impianto detto ferriera o ferrera alla genovese dai suoi stessi creatori. A partire dal XVI secolo essa è presente in tutti i paesi del Mediterraneo – dalla Sicilia al Piemonte, al Delfinato fino ai Paesi Baschi – e risulta aver soppiantato tutti quegli impianti a focolare chiuso – fornelli – da cui si ricavava un massello – blumo – contenente ferro carbone e acciaio da raffinare ulteriormente. La nuova tecnica utilizzava un solo impianto a focolare aperto, del tutto simile a quello utilizzato per la raffinazione della ghisa. Mantici mossi da ruota idraulica alimentavano la combustione di una miscela di minerale e carbone di legna potendo raggiungere una temperatura massima di 1.200 °C. Con la liquefazione della ganga si formava un blumo di ferro spugnoso grazie all'opera di rimescolamento eseguita da un pratico. Con successivi riscaldi e battiture al maglio idraulico il blumo raggiungeva la sua forma definitiva di barra di ferro. Agricola documenta impianti analoghi, ma senza un legame apparente con le ferriere alla genovese, nell'Alto Palatinato alla fine del Quattrocento. Il limite del processo era il dover disporre di un minerale ricco e facilmente fusibile – come è il caso delle ematiti elbane e pirenaiche – e nell'impossibilità di produrre direttamente acciaio. Il suo punto di forza era, oltre il basso impiego di manodopera e capitali, nella produzione di un ottimo ferro malleabile: un fatto di rilievo sia tecnico sia economico che prolungherà la sua esistenza fino alla prima metà dell'Ottocento. La ferriera alla genovese passa da una produzione nel Quattrocento di circa un quintale di ferro nelle 24 ore ai tre quintali (suddivisi in tre masselli) nel secolo successivo. Sul finire del Settecento e fino a metà Ottocento del termine alla genovese si perde la memoria e saranno rinomati gli impianti alla catalana francesi e spagnoli che migliorando il processo e usando magli particolarmente efficienti garantivano produzioni anche di 6 quintali nelle 24 ore. Se oggi si sfoglia un dizionario tecnico catalana è sinonimo di ferriera a riduzione diretta[50].
L'acciaio a pacchetto
[modifica | modifica wikitesto]In Europa la principale tecnica utilizzata fino al X secolo fu quella dell'acciaio a pacchetto, che consentiva di controllare più agevolmente il tenore di carbonio del metallo rispetto a quanto si poteva fare usando l'acciaio omogeneo che pure veniva prodotto, in quantità limitate, dai bassoforni alto-medioevali.
Consiste nel creare un pacchetto di strati alternati di ferro dolce e ghisa, fatti rammollire e poi martellati insieme per saldarli e far diffondere il carbonio dalla ghisa al ferro dolce, in modo da ottenere la percentuale di carbonio desiderata. Una volta saldati gli strati del pacchetto, si taglia la barra e la si piega su sé stessa, ripetendo il processo: in questo modo si possono creare barre estremamente resistenti composte di centinaia o migliaia di strati sottilissimi. È un processo la cui riuscita dipende moltissimo dalla capacità e dall'esperienza del fabbro: è molto difficile ottenere due volte lo stesso risultato con questo metodo in quanto la lunghezza della lavorazione alla forgia, la sua complessità, così come il calore a cui viene riscaldato il pezzo in lavorazione, influenzano il tenore in carbonio dell'acciaio e le caratteristiche meccaniche del pezzo finito.
Il processo è noto in Europa fin dalla tarda epoca dei Celti (dopo che l'uso dei perfezionati bassoforni greci si era diffuso nell'Europa Occidentale), dei quali sono rimaste alcune spade che mostrano una stratificazione di questo genere (per quanto limitata a poche decine di strati). Alla fine dell'età romana era sicuramente noto ai barbari di stirpe germanica, ed è stato per secoli l'unico modo noto, al di fuori dell'India, per ottenere acciaio di buona qualità.
Per secoli l'unico modo di ottenere del buon acciaio in Europa fu quindi quello di usare ferro delle miniere svedesi, particolarmente puro e privo di zolfo e fosforo, "ferro di palude" (limonite), siderite di origine alpina o ematite dell'Isola d'Elba, ed usarlo per confezionare acciaio a pacchetto con ghisa più ricca di carbonio. Era un processo molto lento ed estremamente costoso: per un chilogrammo di acciaio erano necessari circa 100 kg di combustibile. Per questo non era conveniente creare pezzi più grandi di una lama di spada. In genere si usava l'acciaio per creare piccoli manufatti, come punte di freccia, bisturi, coltelli ed altri oggetti di piccole dimensioni.
Per questo motivo durante il basso Medioevo in Europa, all'incirca a partire dal IX secolo, con l'aumentata disponibilità di acciaio omogeneo, che riduceva i tempi di lavorazione, la tecnica dell'acciaio a pacchetto fu progressivamente abbandonata, portando a un generale scadimento della qualità delle lame europee del periodo. Dall'XI secolo al XVI secolo la tecnica cadde completamente in disuso. Venne riscoperta con il Rinascimento, data la maggiore richiesta di lame di qualità superiore e peso inferiore, e in quel periodo molti si convinsero che l'acciaio Damasco, di cui i crociati raccontavano meraviglie, non fosse altro che un tipo di acciaio a pacchetto, ma questa credenza è stata smentita dalle analisi delle nervature visibili nei due tipi di acciaio.
Il processo di "lavorazione a Damasco" è ancora oggi utilizzato per la produzione artigianale di coltelleria e repliche di armi bianche storiche di alta qualità.
I primi forni da ghisa in Europa
[modifica | modifica wikitesto]
In Europa si cominciò a produrre ghisa per fare ferro e acciaio nel basso Medioevo quando furono costruiti forni chiusi con un particolare profilo a imbuto e grazie all'impiego della ruota idraulica ad asse orizzontale utilizzata per azionare i mantici; fu così relativamente facile ottenere e controllare temperature superiori ai 1200 °C (1147 °C temperatura di fusione dell'eutettico della ghisa). La ghisa ottenuta dal forno era rifusa in fucine, anch'esse di nuova concezione, che utilizzavano soffierie idrauliche particolarmente potenti, indispensabili per produrre le alte temperature (1200 °C) necessarie a liquefarla nuovamente per farne getti, ferro e acciaio. Le prime notizie di impianti con tali caratteristiche riguardano il Dalarne-Vestmanland nella Svezia centrale (datati al XIII secolo e poi detti masugn), la Markisches Sauerland, nella Ruhr tedesca (forni da ghisa datati col radiocarbonio fra il 1205 e il 1300, prima menzione scritta Masshutte nel 1311) e il lato meridionale delle Alpi centrali (furnus nel 1179 ad Ardesio e furnus e fuxina a Schilpario nel 1251 e a Semogo nel 1286)[51].
Processi di affinamento
[modifica | modifica wikitesto]Un metodo alternativo di decarburizzare la ghisa grezza sembra essere stato ideato nella regione attorno a Namur nel XV secolo. Questo processo vallonico si diffuse alla fine del secolo fino al Pay de Bray, sul confine orientale della Normandia, e poi verso la Gran Bretagna, dove divenne il metodo principale per la fabbricazione del ferro battuto nel 1600. Fu introdotto in Svezia da Louis de Geer all'inizio del XVII secolo e fu usato per fabbricare il ferro di Oreground (dal nome della cittadina Svedese di Öregrund).
Una variazione di questo era il procedimento tedesco. Divenne il metodo principale per produrre il ferro battuto in Svezia.
L'acciaio Bulat
[modifica | modifica wikitesto]L'acciaio Bulat (dalla parola persiana pulad, acciaio) fu inventato da Pavel Petrovich Anosov, dopo anni di studi sulla perduta arte dell'acciaio Damasco di cui Anosov voleva riscoprire il segreto. L'acciaio Bulat era un acciaio stratificato, ottenuto raffreddando molto lentamente la massa fusa in modo che il carbonio si potesse concentrare in strati diversi: in questo modo il metallo finale consisteva di molti strati di ferrite (acciaio dolce) e perlite (acciaio duro).
La perlite però è instabile a temperature superiori a 727 °C e tende a scomporsi in ferrite e austenite, per trasformarsi di nuovo al raffreddamento, motivo per cui la lavorazione a caldo di questo tipo di acciaio richiedeva particolare attenzione.
L'acciaio cementato
[modifica | modifica wikitesto]All'inizio del XVII secolo, i siderurgisti nell'Europa Occidentale trovarono un modo (chiamato cementazione) per carburare il ferro battuto. Le barre in ferro e il carbone venivano messi dentro scatole in pietra, poi mantenute a una temperatura rossa (la temperatura a cui il ferro diviene leggermente luminescente e "rosso") fino a una settimana. In questo periodo, il carbonio diffonde nel ferro, producendo un materiale chiamato acciaio cementato o acciaio a bolle. A Coalbrookdale, in Inghilterra, si trovano due fornaci per la cementazione utilizzate da Sir Basil Brooke, che tenne il brevetto sul processo tra il 1610 e il 1619.
La qualità dell'acciaio poteva essere migliorata lavorandolo tramite la piegatura su sé stesso, producendo acciaio a strati. Tuttavia nel periodo tra il 1740 e il 1750 Benjamin Huntsman trovò un modo di fondere nei crogioli l'acciaio cemento ottenuto dal processo di cementazione.
Sviluppo delle fonderie alimentate idraulicamente
[modifica | modifica wikitesto]A volte, nel periodo medioevale, l'energia dell'acqua era applicata ai processi delle fonderie. È possibile che questo avvenne presso l'Abbazia di Clairvaux dell'Ordine Cisterciense nel 1135, ma fu certamente in uso in Francia e in Svezia all'inizio del XIII secolo.[52] In Inghilterra, le prime chiare prove documentate di questo furono nella contabilità di una forgia del Vescovato di Durham, vicino a Bedburn nel 1408,[53] ma non fu certamente la prima volta che venivano impiegate simili tecniche siderurgiche. Nel distretto inglese di Furness, le fonderie alimentate idraulicamente furono in uso all'inizio del XVIII secolo, e vicino a Garstang fino al 1770 circa.
La forgia catalana è un tipo di fonderia alimentata. Le fonderie con il "soffio caldo" erano usate nello Stato di New York a metà del XIX secolo.
L'invenzione del carbon coke
[modifica | modifica wikitesto]
Fondamentale fu l'introduzione del coke, avvenuta nel Settecento in Inghilterra. "Cuocendo" il carbone (ovvero scaldandolo in assenza di ossigeno) si otteneva carbone "cooked" o coke. Il coke venne utilizzato negli altoforni al posto del carbone di legna, permettendo di incrementare la produzione di ghisa grezza.
Le prime fusioni del ferro usavano il carbone vegetale sia come sorgente di calore che come agente di riduzione. Nel XVIII secolo la disponibilità di legno per il carbone limitava l'espansione della produzione del ferro e l'Inghilterra divenne sempre più dipendente, per una parte considerevole del ferro richiesto dalle sue industrie, dalla Svezia (dalla metà del XVII secolo) e poi dal 1725 anche dalla Russia.[54]
La fusione tramite carbon fossile (o il suo derivato carbon coke) era un obiettivo cercato da tempo. La produzione della ghisa grezza con il coke fu probabilmente ottenuta da Dud Dudley nel 1620, e con un mix di carburanti fatto con carbon fossile e legno nel 1670. Questo fu però probabilmente soltanto un successo tecnologico e non commerciale. Shadrach Fox potrebbe aver fuso il ferro con il coke presso Coalbrookdale in Shropshire nel 1690, ma soltanto per fare palle di cannone ed altri prodotti in ghisa come gusci. Tuttavia, nella pace seguita alla guerra dei nove anni, non ci fu una sufficiente domanda di queste.[55]
Abraham Darby e i suoi successori
[modifica | modifica wikitesto]Nel 1707, Abraham Darby I brevettò un metodo per la fabbricazione di pentole in ghisa; tali pentole erano più sottili e quindi più economiche di quelle della concorrenza. Avendo bisogno di una quantità maggiore di ghisa grezza, egli noleggiò l'altoforno di Coalbrookdale nel 1709. Là, egli fabbricò il ferro utilizzando il coke, stabilendo di conseguenza il primo commercio di successo di questo genere in Europa. Lo sviluppo del suo metodo che prevedeva di caricare il forno con coke e minerale di ferro, porterà alla tecnologia degli altoforni alimentati a coke che tuttora è quella utilizzata. I suoi prodotti erano tutti in ghisa, anche se i suoi successori più immediati tentarono (con piccolo successo commerciale) di affinarlo in ferro (puro) in barre.[56]
Il ferro in barre continuò di conseguenza ad essere fabbricato con ghisa grezza al carbone vegetale fino al 1755. In questo anno Abraham Darby II (e soci) aprirono una nuova fornace funzionante con il coke presso Horsehay in Shropshire e fu presto imitato da altri. Questi procurarono ghisa grezza al coke alle forge di affinatura di tipo tradizionale per la produzione di ferro battuto. La ragione di questo ritardo rimane controversa[57] anche se probabilemnete dovuta ad una serie di cause. In effetti, almeno inizialmente il coke presentava un costo maggiore del carbone vegetale e lasciava nella ghisa un eccesso di silicio rendendola di cattiva qualità[58] ed altre difficoltà tecniche che necessitarono di tempo per essere risolte.
La reinvenzione dell'acciaio al crogiolo
[modifica | modifica wikitesto]Nel 1740 Benjamin Huntsman, a Sheffield, riscoprì la tecnica dell'acciaio al crogiolo. Dopo anni di esperimenti in segreto, mise a punto una fornace in grado di raggiungere i 1600 °C in cui metteva una dozzina di crogioli di argilla, ciascuno con 15 kg di ferro, che veniva portato lentamente al calor bianco; a questo punto si aggiungevano pezzi di ghisa, i quali, lasciati fondere, aggiungevano al materiale il carbonio necessario; dopo tre ore circa l'acciaio fuso veniva colato in lingotti.
Nel 1740 Sheffield produceva circa 200 tonnellate di acciaio all'anno; un secolo dopo ne produceva 80.000, la metà di tutta la produzione europea, ed era la più grande città industriale d'Europa.
Questo modo di produrre l'acciaio dominò fino all'arrivo del convertitore Bessemer, che produceva acciaio di qualità comparabile ma con costi minori.
Nuovi processi di forgiatura
[modifica | modifica wikitesto]
Fu soltanto dopo questi avvenimenti che cominciarono ad essere concepiti modi attuabili economicamente per convertire la ghisa grezza in ferro. Un processo conosciuto come invasatura e stampaggio fu ideato nel 1760 e migliorato nel 1770, e sembra essere stato ampiamente adottato nelle Midlands occidentali circa dal 1785. Tuttavia, questo metodo fu rimpiazzato dal processo di affinatura di Henry Cort, brevettato nel 1784, ma probabilmente fatto funzionare con ghisa grezza grigia circa nel 1790. Questi processi permisero la grande espansione della produzione del ferro che costituì la Rivoluzione industriale per l'industria del ferro.[59]
All'inizio del XIX secolo, Hall scoprì che l'aggiunta di ossidi di ferro al contenuto dei forni di affinatura provocava una violenta reazione, nella quale la ghisa grezza veniva decarburizzata; questo processo venne chiamato 'affinatura umida'. Si scoprì anche che era possibile produrre acciaio fermando il processo di affinatura prima che la decarburizzazione fosse completa.
Vento caldo
[modifica | modifica wikitesto]L'efficienza dell'altoforno fu migliorata dall'innovazione del "vento caldo" (l'aria, prima di entrare nella fornace, veniva preriscaldata), brevettato da James Beaumont Neilson in Scozia nel 1828. Questo ridusse ulteriormente i costi di produzione. Nel giro di pochi decenni, l'abitudine divenne quella di avere una 'stufa' grande quanto la fornace vicino ad essa, nella quale i gas d'altoforno (contenenti CO, monossido di carbonio) provenienti dalla fornace venivano diretti e bruciati. Il calore risultante veniva usato per preriscaldare l'aria soffiata nella fornace.[60]
Il forno Martin-Siemens
[modifica | modifica wikitesto]
Negli anni 1850 Sir Carl Wilhelm Siemens ideò il cosiddetto forno Siemens, che rispetto alle metodologie precedenti riusciva a diminuire i consumi di combustibile del 70-80%.
Nel 1865 l'ingegnere francese Pierre-Emile Martin acquistò il brevetto e introdusse l'uso del forno Siemens (che da quel momento in poi fu chiamato "forno Martin-Siemens") per svolgere l'ossigenazione della ghisa grezza (in inglese pig iron).
L'invenzione del convertitore
[modifica | modifica wikitesto]
A parte una qualche produzione di acciaio affinato, l'acciaio Inglese continuò ad essere fabbricato tramite cementazione, a volte seguita da rifusione per produrre acciaio in crogiolo. Questi erano processi "in lotto" la cui materia prima era il ferro (puro) in barre, in particolare il ferro di Oregrund in Svezia.
Il problema della produzione in massa di acciai economici fu risolto nel 1855 da Henry Bessemer, con l'introduzione del convertitore Bessemer nella sua fabbrica di Sheffield in Inghilterra.[61] Nel convertitore Bessemer, la ghisa grezza fusa proveniente dall'altoforno veniva inserita in un grosso crogiolo e poi veniva soffiata aria dal basso attraverso il materiale fuso, bruciando il carbonio disciolto dal coke. Mano a mano che il carbonio brucia, il punto di fusione del materiale aumenta, ma il calore proveniente dal carbonio in fiamme procura l'energia in più necessaria a mantenere il miscuglio fuso. Dopo che il contenuto in carbonio nella colata ha raggiunto il livello desiderato, il flusso d'aria può essere chiuso. Un tipico convertitore Bessemer poteva convertire un lotto di 25 tonnellate di ghisa grezza in acciaio in mezzora circa. L'invenzione dei convertitori ad aria, primo fra i quali il convertitore Bessemer, permise di abbandonare il metodo del pudellaggio (acciaio al crogiolo), lungo e dispendioso.
L'acciaio inox
[modifica | modifica wikitesto]Vi furono innumerevoli tentativi svolti nel XIX secolo, tesi ad ottenere una lega che mantenesse le caratteristiche meccaniche dell'acciaio risultando però inossidabile. Le varie sperimentazioni si orientarono verso l'aggiunta nell'acciaio di cromo, nichel ed altri metalli[62]. Nel 1913 l'inglese Harry Brearly riuscì ad ottenere effettivamente l'acciaio inossidabile mediante un'alta percentuale di cromo.[63]
I convertitori a ossigeno
[modifica | modifica wikitesto]Nel 1952 venne poi introdotto alla Voest-Alpine il processo di ossigenazione,[64][65] una modifica al processo Bessemer, che lancia ossigeno da sopra all'acciaio (invece che soffiare aria da sotto), riducendo la quantità di azoto incluso nell'acciaio. Questo processo viene usato in tutte le fabbriche di acciaio attuali; l'ultimo convertitore Bessemer degli Stati Uniti venne messo a riposo nel 1968. Inoltre, a partire dagli anni seguenti la seconda Guerra Mondiale, a Brescia (Italia), utilizzando solo rottami di ferro fusi nel forno elettrico ad arco, iniziarono a produrre acciaio dei piccoli stabilimenti chiamati ironicamente mini-acciaierie. Queste fabbriche producevano solo prodotti in barre all'inizio, ma si sono poi espansi a prodotti piatti e pesanti, una volta dominio esclusivo dei circuiti della fabbricazione dell'acciaio integrata.
Prima di questi sviluppi del XIX secolo, l'acciaio era un lusso costoso e veniva usato solo per un numero limitato di scopi nei quali era necessario un metallo particolarmente duro o flessibile, come nelle parti taglienti degli attrezzi e nelle molle. La grande diffusione di acciaio poco costoso alimentò la seconda rivoluzione industriale e la società moderna come la conosciamo. L'acciaio dolce ha rimpiazzato il ferro battuto per quasi tutti gli scopi, e quest'ultimo non viene più (o quasi più) fabbricato. Con piccole eccezioni, le leghe di acciaio cominciarono ad essere prodotte solo nel tardo XIX secolo. L'acciaio inossidabile fu sviluppato solo all'alba della prima guerra mondiale e divenne largamente usato soltanto negli anni 1920. Queste leghe di acciaio sono tutte conseguenza della grande disponibilità di ferro ed acciaio a basso costo e della possibilità di legarli a volontà.
Nel 1992 il processo Martin-Siemens era definitivamente soppiantato negli Stati Uniti d'America dai convertitori a ossigeno (come il convertitore Bessemer e il processo Linz-Donawitz[66]). La nazione con la percentuale più alta di acciaio prodotto a mezzo del processo Martin-Siemens (circa il 50%) rimane l'Ucraina.[67]
Note
[modifica | modifica wikitesto]- ^ Archeometallurgia del ferro, su archeologiamedievale.unisi.it. URL consultato il 26 marzo 2009 (archiviato dall'url originale il 1º aprile 2009).
- ^ L'aggettivo "ponderale" fa riferimento al termine "concentrazione in massa" o "percentuale in massa", con il quale si indica la concentrazione espressa dal rapporto tra la massa del componente in miscela e la massa totale della miscela, moltiplicato per 100.
- ^ Enzo Baraldi, Una nuova età del ferro: macchine e processi della siderurgia, in Il Rinascimento italiano e l'Europa, Volume III: Produzioni e tecniche, Treviso, Angelo Colla editore, 2007. ISBN 978-88-89527-17-7.
- ^ Copia archiviata (PDF), su museoitalianoghisa.org. URL consultato il 26 marzo 2009 (archiviato dall'url originale il 17 giugno 2012).
- ^ Benvéniste 1969 cit. dep; Rick Mc Callister and Silvia Mc Callister-Castillo, Etruscan Glossary, su etruscans1.tripod.com, 1999. URL consultato il 19 giugno 2006.
- ^ Online etymology dictionary, su etymonline.com.
- ^ myEtymology.com: English etymology of iron
- ^ IF 46:184f
- ^ "Pietre cadute dal cielo" - Meteoriti al Planetario di Torino Archiviato il 15 febbraio 2009 in Internet Archive.
- ^ R. F. Tylecote, A History of Metallurgy (2nd edn, 1992), 3
- ^ Meteoriti Archiviato il 19 ottobre 2012 in Internet Archive.
- ^ Girolamo Zampieri, "Bronzi antichi", L'erma di Bretschneider editore, 2000, ISBN 88-8265-117-7 p.113
- ^ T. A. Rickard, The Use of Meteoric Iron, in The Journal of the Royal Anthropological Institute of Great Britain and Ireland, vol. 71, n. 1/2, 1941, pp. 55–66., DOI:10.2307/2844401.
- ^ Buchwald, V F, On the Use of Iron by the Eskimos in Greenland, in Materials Characterization, vol. 29, n. 2, 1992, pp. 139–176, DOI:10.1016/1044-5803(92)90112-U.
- ^ Meteoritical Bulletin, no. 28, Moscow (1963)
- ^ Anatomia nell'Iliade di Omero
- ^ "Iliade di Omero", traduzione di Vincenzo Monti
- ^ Monica Pugliara, "Il mirabile e l'artificio"
- ^ E. Photos, "The Question of Meteoritic versus Smelted Nickel-Rich Iron: Archaeological Evidence and Experimental Results" World Archaeology Volume 20, Numero 3, Archaeometallurgy (febbraio 1989), pp. 403-421.
- ^ Waldbaum, Jane C. From Bronze to Iron. Göteburg: Paul Astöms Förlag (1978): 56-8.
- ^ Breve storia del Ferro, su zoomedia.it.
- ^ a b Waldbaum 1978: 23.
- ^ a b c d Muhly, James D. 'Metalworking/Mining in the Levant' pp. 174-83 in Near Eastern Archaeology ed. S. Richard Winona Lake, IN: Eisenbrauns (2003): 180.
- ^ Cosa è l'acciaio damascato
- ^ Comi Ivano, "Acciaio Damasco", 1996, Hoepli editore. ISBN 88-203-2297-8
- ^ a b The origins of Iron Working in India: New evidence from the Central Ganga plain and the Eastern Vindhyas by Rakesh Tewari (Director, U.P. State Archaeological Department)
- ^ a b Marco Ceccarelli (2000). International Symposium on History of Machines and Mechanisms: Proceedings HMM Symposium. Springer. ISBN 0-7923-6372-8. pp 218
- ^ a b I. M. Drakonoff (1991). Early Antiquity. University of Chicago Press. ISBN 0-226-14465-8. pp 372
- ^ J. F. Richards et al (2005).The New Cambridge History of India. Cambridge University Press. ISBN 0-521-36424-8. pp 64
- ^ Patrick Olivelle (1998). Upanisads. Oxford University Press. ISBN 0-19-283576-9. pp xxix
- ^ a b G. Juleff, An ancient wind powered iron smelting technology in Sri Lanka, in Nature, vol. 379, n. 3, 1996, pp. 60-63, DOI:10.1038/379060a0.
- ^ Katharine Sanderson, Sharpest cut from nanotube sword: Carbon nanotech may have given swords of Damascus their edge, Nature, 15 novembre 2006. URL consultato il 17 novembre 2006.
- ^ Suspension bridge. (2007). In Encyclopedia Britannica. Retrieved April 5, 2007, from Encyclopedia Britannica Online
- ^ Delhi Iron Pillar: New Insights. R. Balasubramaniam, Delhi: Aryan Books International and Shimla: Indian Institute of Advanced Studies, 2002, Hardbound, ISBN 81-7305-223-9. Review: Delhi Iron Pillar: New InsightsLIST OF PUBLICATIONS ON INDIAN ARCHAEOMETALLURGY
- ^ Roy Porter (2003). The Cambridge History of Science. Cambridge University Press. ISBN 0-521-57199-5. pp 684
- ^ Needham, Volume 4, Part 2, 544 g
- ^ Woods, 49-50.
- ^ Wagner, 52.
- ^ Needham, Volume 4, Part 3, 197.
- ^ Needham, Volume 4, Part 3, 277.
- ^ Needham, Volume 4, Part 3, 563 g
- ^ Needham, Volume 4, Part 3, 86.
- ^ Needham, Volume 4, Part 1, 282.
- ^ Needham, Volume 4, Part 2, 370
- ^ a b Needham, Volume 4, Part 2, 371-372.
- ^ Needham, Volume 4, Part 2, 373.
- ^ Robert Hartwell, 'Markets, Technology and the Structure of Enterprise in the Development of the Eleventh Century Chinese Iron and Steel Industry' Journal of Economic History 26 (1966). pp. 53-54
- ^ a b Ebrey, 158.
- ^ a b Needham, Volume 4, Part 2, 376.
- ^ Enzo Baraldi, La “ferriera alla genovese” tra XIV e XVII secolo, in: Pratiche e Linguaggi. Contributi a una storia della cultura tecnica e scientifica, Edizioni ETS 2005
- ^ Enzo Baraldi, Una nuova età del ferro: macchine e processi della siderurgia, in Il Rinascimento italiano e l'Europa, Volume III: Produzioni e tecniche, Treviso, Angelo Colla editore, 2007. ISBN 978-88-89527-17-7
- ^ A. R. Lucas, 'Industrial milling in the ancient and Medieval Worlds' Technology and Culture 46 (2005), 19.
- ^ R. F. Tylecote, A History of Metallurgy, 76.
- ^ P. W. King, 'The production and consumption of bar iron in early modern England and Wales' Economic History Review 58(1) (2005), 1-33.
- ^ P. W. King, 'Dud Dudley's contribution to metallurgy' Historical Metallurgy 36(1) (2002), 43-53; P. W. King, 'Sir Clement Clerke and the adoption of coal in metallurgy' Trans. Newcomen Soc. 73(1) (2001-2), 33-52.
- ^ A. Raistrick, A dynasty of Ironfounders (1953; 1989); N. Cox, 'Imagination and innovation of an industrial pioneer: The first Abraham Darby' Industrial Archaeology Review 12(2) (1990), 127-144.
- ^ A. Raistrick, Dynasty; C. K. Hyde, Technological change and the British iron industry 1700-1870 (Princeton, 1977), 37-41; P. W. King, 'The Iron Trade in England and Wales 1500-1815' (Ph.D. thesis, Wolverhampton University, 2003), 128-41.
- ^ S. Ciriacono, La rivoluzione industriale: dalla protoindustrializzazione alla produzione flessibile, 2000
- ^ G. R. Morton and N. Mutton, 'The transition to Cort's puddling process' Journal of Iron and Steel Institute 205(7) (1967), 722-8; R. A. Mott (ed. P. Singer), Henry Cort: The great finer: creator of puddled iron (1983); P. W. King, 'Iron Trade', 185-93.
- ^ A. Birch, Economic History of the British Iron and Steel Industry , 181-9; C. K. Hyde, Technological Change and the British iron industry (Princeton 1977), 146-59.
- ^ Uno dei primi convertitori è ancora visibile presso il Kelham Island Museum nella città.
- ^ G.Di Caprio, Gli acciai inossidabili, 2003
- ^ http://www.mbmitalia.com/new/userimages/AcciaioStoria.pdf
- ^ In inglese è chiamato Basic oxygen steelmaking (BOS), Basic Oxygen Furnace (BOF), Linz-Donawitz-Verfahren, o LD-converter.
- ^ McGannon, Harold E. editore (1971). The Making, Shaping and Treating of Steel: Ninth Edition. Pittsburgh, Pennsylvania: United States Steel Corporation, p.26
- ^ Detto anche "Processo LD".
- ^ 41724.PDF (PDF), su energystar.gov. URL consultato il 4 maggio 2019 (archiviato dall'url originale il 9 agosto 2017).
Bibliografia
[modifica | modifica wikitesto]- Ernesto Salamoni, Dal ferro all'acciaio, Editori Riuniti, 1994, ISBN 88-359-2576-2.
- Mauro Cavallini, Fortuitum & sordidum opus. Appunti di storia della metallurgia, CRACE, 2005, ISBN 88-87288-58-5.
- Andrea Raggi, Barbara Paparo, Giancarlo Barbiroli, Mutamenti tecnologici e strutturali nell'industria siderurgica mondiale. Un modello altamente innovativo, 2ª ed., Edizioni Franco Angeli, 2000, ISBN 88-464-0046-1.
- Massimo Paoli, Struttura e progresso tecnologico della industria siderurgica. Il caso italiano, 1ª ed., Edizioni Franco Angeli, 1984, ISBN 88-204-4163-2.
- Angelo Nesti, La siderurgia toscana nel XVIII secolo, Felici Editore, 2005, ISBN 88-88327-97-5.
- Bay Fernand, Paesaggi industriali del Novecento. Siderurgia e miniere nella Maremma Toscana., a cura di Massimo Preite, Polistampa Editore, 2006, ISBN 88-596-0140-1.
- (EN) Patricia Buckley Ebrey, Anne Walthall, James B. Palais, East Asia: A Cultural, Social, and Political History, 1ª ed., Wadsworth Publishing, 2005, ISBN 0-618-13384-4.
- (EN) Michael Woods, Mary B. Woods, Ancient Machines: From Wedges to Waterwheels (Ancient Technology), Runestone Press, 1999, ISBN 0-8225-2994-7.
- (EN) Donald B. Wagner, Iron and Steel in Ancient China, E. J. Brill, 1993, ISBN 90-04-09632-9.
- (EN) Radomír Pleiner, Iron in Archaeology: The European Bloomery Smelters, Archeologický Ústav Av Cr., Praga, 2000, ISBN 978-80-86124-26-1.
- (EN) Joseph Needham, Science and Civilization in China: Volume 4, Part 2, Caves Books, Ltd., Taipei, 1986.
- (EN) Joseph Needham, Science and Civilization in China: Volume 4, Part 3, Caves Books, Ltd., Taipei, 1986.
- Oleg D. Serby e Joffrey Wadsworth, Gli acciai di Damasco, in: Le scienze, nº 200, aprile 1985.
- Rosario Pinto, Il Paesaggio industriale, Print Art Edizioni, Nocera Superiore, 2016, 9788898887200
Voci correlate
[modifica | modifica wikitesto]- Siderurgia
- Ferro
- Acciaio
- Ghisa
- Metallurgia
- Centro siderurgico
- Altoforno
- Corex
- Fonderia
- Storia dell'industria italiana
- Ferriera alla genovese
- Tromba idroeolica
Altri progetti
[modifica | modifica wikitesto]Wikimedia Commons contiene immagini o altri file su storia della siderurgia
Collegamenti esterni
[modifica | modifica wikitesto]- Età del ferro (PDF), su scuoladecs.ti.ch.
- Ferro, acciai e ghise (PDF), su reolab.unimo.it. URL consultato il 1º febbraio 2009 (archiviato dall'url originale il 13 giugno 2010).
- Produzione di acciaio, su infobuilddossier.it (archiviato dall'url originale il 28 novembre 2011).
- L'età del ferro (PDF), su scuoladecs.ti.ch.
- Filmato didattico e interattivo sull'acciaio" (SWF), su promozioneacciaio.it. URL consultato il 30 giugno 2011 (archiviato dall'url originale il 19 aprile 2015).